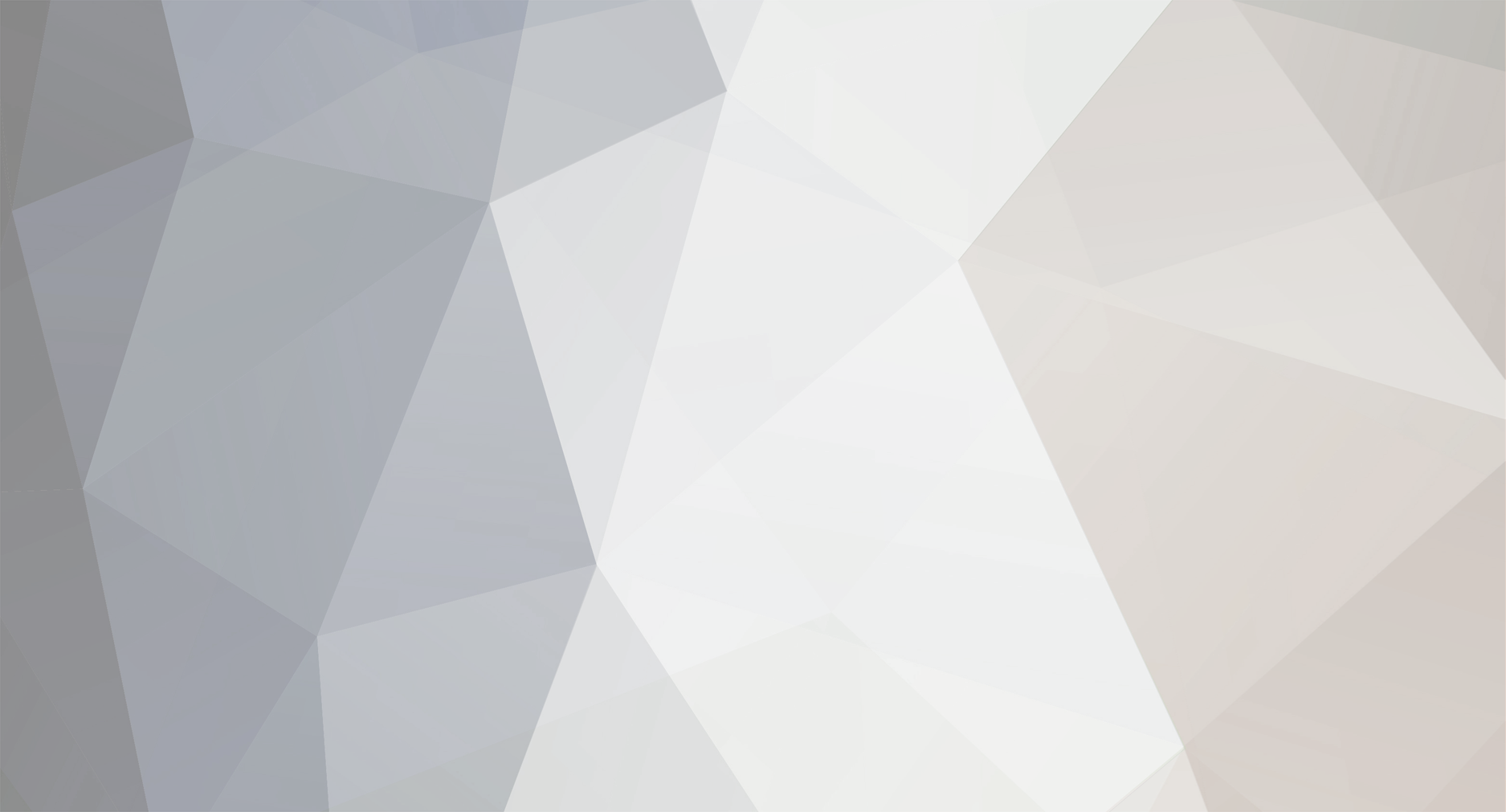
foster9099
Members-
Content Count
30 -
Joined
-
Last visited
Content Type
Profiles
Forums
Blogs
Calendar
Articles
Gallery
Downloads
Store
Everything posted by foster9099
-
You might have noticed the 45 degree bend intercooler pipe that I had originally put on. When I tried to test fit the air filter there was nowhere for the filter to go, I then knew I had 2 options, find a new way of running the intercooler piping or relocate the battery. As it happened a friend has a load of off cut bends of 2.25" stainless steel, I can weld stainless and create a much better fitting pipe run. [ATTACH=CONFIG]96982[/ATTACH] This is what we came up with, the intercooler piping going down underneath where the air filter will sit. [ATTACH=CONFIG]96983[/ATTACH] Here is the pipe joining up to the intercooler. Im very pleased with how this turned out. Now i just need to get a couple of fittings, one for the N75 valve and one for the re-circulation valve.
-
Just visually it looks really good actually, the pins fit perfectly in the holes on the lower cross member. The top bracket fits into a little slot just like the original. It comes with a plug in the bottom which I removed to screw in the sensor. So actually for the price i'm pretty impressed with it, the real test will be when I get to running the car.
-
Once I had all the plumbing for the turbo sorted out I fitted my refurbished one [ATTACH=CONFIG]96972[/ATTACH] When I went ahead and compared the 2 turbos side by side, my refurbished turbo has a bigger inlet when is interesting. The turbo on the left (refurbished) was the turbo the previous owner had on the car when it was remapped and when the engine was at its best. They changed the turbo to the one on the right when they had engine failure on the previous engine, they told me that the car was never quite the same afterwards. [ATTACH=CONFIG]96973[/ATTACH] The engine with all the accessories attached. [ATTACH=CONFIG]96974[/ATTACH] The clutch and flywheel was in good condition, the clutch actually didn't look that old but it did slip on me a couple of times. I took everything up to CG Motorsport in Leeds to get something that would handle the extra power. They rebuild the clutch plate to a dual friction material, this is organic on one side and paddle on the other. They also refinished the flywheel and pressure plate and gave it all a coat of paint. Sadly I didn't remember to take a photo of the clutch before it all went together. [ATTACH=CONFIG]96975[/ATTACH] Gearbox on and ready to drop in the car. [ATTACH=CONFIG]96976[/ATTACH] Back in the car. [ATTACH=CONFIG]96977[/ATTACH] At this stage all the engine wiring has been connected and the radiator is test fitted with the top cross member. [ATTACH=CONFIG]96978[/ATTACH] The previous intercooler and piping arrangement was a mess so i'm going to be re-engineering the whole setup. I have some bits of silicone joiners and piping but I will be needing more, I didn't realise how expensive even a simple 90 degree joiner is. Adding all the piping bits I need its easy for it to add up to £50 £60. The image shows the small gap that I have to fit my piping through, there is enough room and it massively simplifies the whole setup compared to what it used to be. The intercooler only just has enough room to fit between the top cross member and the power steering cooler.
-
I was tempted to build this engine but it ran well before apart from the turbo and I want to be driving the car this summer. My plan is to get another engine and rebuild that, most likely with forged rods, while still been able to drive the car.
-
Time to make a start on the engine, i'm not going to tear down this engine and rebuild it but i will clean it up and replace some seals and gaskets etc. [ATTACH=CONFIG]96904[/ATTACH] First is the sump off, there was far too much rtv used previously. I have also removed the pickup and the plastic baffle in this image. [ATTACH=CONFIG]96905[/ATTACH] There is some bits of metal in the pickup, not really sure what they are from but I cant find any evidence of catastrophe. The pickup and o ring will be replaced with a new genuine part. [ATTACH=CONFIG]96906[/ATTACH] Side note, I finally got the track rod boots. The picture was taken before I got the tool to crimp the retaining clips on. [ATTACH=CONFIG]96907[/ATTACH] I did a quick clean of the engine block and laid down the first coat of paint, I wasn't too worried about the finish as I think I will end up with a different engine at some point to completely rebuild. [ATTACH=CONFIG]96908[/ATTACH] Another side note, managed to get the brake booster/ servo installed. Its a pain to get it lined up while fitting it between the strut tower, a second person inside the car makes the job a little easier. [ATTACH=CONFIG]96909[/ATTACH] The oil filter housing and oil cooler were cleaned up and painted black and the alternator bracket painted yellow. I began to fit everything back to the engine including the thermostat and knock sensors. [ATTACH=CONFIG]96910[/ATTACH] [ATTACH=CONFIG]96913[/ATTACH] This is a mock fitment of the exhaust/ turbo system to help me remember where everything goes. The turbo is a Chinese K04-001 which is supposed to be a bit of a hybrid K03s, however with Chinese quality. This turbo was supposed to be fairly new when I got the car back end of summer last year, by the time I took it off the road the car was smoking quite bad and losing coolant so I suspect the seals in the turbo are gone. I did have a spare K04-001 turbo that came with the car, I had this spare turbo refurbished by a reputable company who fitted new seals, uprated journal bearings and a billet K04 compressor wheel. [ATTACH=CONFIG]96911[/ATTACH] This was him showing me the difference between the old parts to the new, you can see the oil galleries are much larger in the new parts. [ATTACH=CONFIG]96912[/ATTACH] This is my refurbished turbo, I will be fitting this once I am confident everything else is in place.
-
[ATTACH=CONFIG]96785[/ATTACH] I bought the parts a while ago to rebuild the shifter mechanism, mainly because the centering spring was snapped and made it very hard to select 3rd gear. I bought all the bushes and spring required direct from VW which came to a massive £6 in total. I decided to tackle this job after watching a very useful video on Youtube, I can post the link if anyone is interested. [ATTACH=CONFIG]96786[/ATTACH] The biggest fear it seems is whether this guide bushing that locks into reverse is intact, mine seemed to look pretty good. I don't have any more photos of the process but it is all fairly simple. [ATTACH=CONFIG]96787[/ATTACH] This is the second time the sub-frame went in, first time was the anti roll bar was the wrong way up and therefore hit the steering arms. I will need to lower the sub-frame slightly again as it seems to be impossible to reattach the steering U joint with the sub-frame all the way up. I also still need to install the rubber boots on the steering rack. [ATTACH=CONFIG]96789[/ATTACH] Test fitted the brand new washer bottle all the way from china, the old one looked pretty disgusting. [ATTACH=CONFIG]96788[/ATTACH] The latest delivery is a shiny aluminium radiator designed to fit in place of the original Corrado one, my original one looked in bad condition and probably wasn't helping the much more powerful engine much.
-
[ATTACH=CONFIG]96761[/ATTACH] I pulled the sub-frame mainly to make it easier to remove the exhaust down pipe and to make it possible to replace the anti roll bar bushes, while the sub-frame is out I will be cleaning and painting everything. [ATTACH=CONFIG]96762[/ATTACH] I used Gunk degreaser which is basically just kerosene and a jet wash to remove pretty much all the muck and grease that was on the sub-frame, ARB and steering rack. I did wire wheel most of the rust away where i could reach but I am painting with Hammerite type paint which can be painted over light rust anyway, plus these parts are mostly hidden when installed so I wasn't too worried. [ATTACH=CONFIG]96763[/ATTACH] Here are all the parts painted up looking fresh. [ATTACH=CONFIG]96764[/ATTACH] A close up of the sub-frame, brush marks are visible but again i'm not too worried at this stage, the point is mainly the muck and grease is gone and they will look clean and fresh for that little glimpse you get when looking into the engine bay. [ATTACH=CONFIG]96765[/ATTACH] Here is the current state of the engine bay, I did pull the front cross member as well which I will give the same treatment as the sub frame. I cleaned the firewall with the Gunk kerosene because I was worried about masking for paint, the paint is actually in pretty good condition so I think I will just leave it as is for now.
-
[ATTACH=CONFIG]96668[/ATTACH] We went to the NEC Practical Classics show and I managed to find this for sale on one of the stands, My plan is to strip it and paint the body with the same Dragon Green colour match paint i've been using in the engine bay. [ATTACH=CONFIG]96669[/ATTACH] I seal sealed the welds on the drivers side inner wing [ATTACH=CONFIG]96670[/ATTACH] I started with the wire wheel on the drivers side sill and unfortunately found the inevitable rust hole, although nowhere near as bad as the passenger side. I think that most of the mess on the sills is caused by someone in the past jacking the car up in the wrong place causing damage to the original underseal. [ATTACH=CONFIG]96671[/ATTACH] After getting bored or wire wheeling the underside I continued preparing the drivers side engine bay for paint [ATTACH=CONFIG]96672[/ATTACH] Filler primer [ATTACH=CONFIG]96673[/ATTACH] Then colour, this is the first coat and I ran out of paint. At the point this photo was taken the colour was still patchy, it looks much better now I just haven't got a photo yet. [ATTACH=CONFIG]96674[/ATTACH] While waiting for the paint to dry I needed a job that didn't create any mess or dust. I managed to get more of the interior installed and its looking more like a car again. I'm still hoping to drive the car this summer.
-
[ATTACH=CONFIG]96626[/ATTACH] I knew the drivers side inner wing was a bit rusty but over the weekend it went over it with a wire wheel on my grinder and it actually turned out to be a lot worse than I thought. I was able to jab a screwdriver through most of this section by hand which shows how weak a lot of the metal was. I actually pulled most of the metal out with pliers and then tidied up the edge with the grinder, I got carried away with it before I remembered to take a photo. Just after this photo I grinded back the rusty part in the foreground and managed to plug weld some of it as you can tell in the second photo. [ATTACH=CONFIG]96627[/ATTACH] The length of that piece of sheet was the maximum width I had, there is still the gap in the foreground that needs to be plated over to finish the job. For the most part I think this fix will do fine even though its a bit ugly, it will be covered by the outer wing anyway.
-
I haven't posted in a little while mainly because I was doing bits and bobs and not really taking many photos. I did manage to get the welding on the passenger sill done and I started to seal seal the welds as well as spreading it out to double up as underseal. [ATTACH=CONFIG]96580[/ATTACH] This is a photo is where i'm at with the welding. The front is done all the way to the middle of the sill. While the car is in the garage forwards i'm concentrating on the front of the car. There will be a little bit of welding at the rear of the sill but that wont be for a while. As you can see there are parts further into the floor where i have undersealed. This is places where the original underseal had been disturbed, i wire wheeled it off and applied new underseal. [ATTACH=CONFIG]96581[/ATTACH] I had taken the seats into the house to protect them from all the welding and grinding in the garage. Yesterday i thought i would have a go and finding out why the drivers seat bolster was sagging, I was expecting to have to find a replacement foam section or even try and make one. [ATTACH=CONFIG]96582[/ATTACH] What I found was the foam to be in relatively good condition and it was in fact the metal support that was completely snapped at the welds. [ATTACH=CONFIG]96583[/ATTACH] From another angle [ATTACH=CONFIG]96584[/ATTACH] So I took the seat back down to the garage (They are not light)and welded the bracket back to the seat base. I used some metal sheet to protect the rest of the seat from the heat and any splatter. [ATTACH=CONFIG]96585[/ATTACH] From another angle, it was really hard to get the mig torch down the back side of the bracket. I probably went overkill with the amount of weld but I figured that I don't want this to break again. [ATTACH=CONFIG]96586[/ATTACH] A bit of galv spray to protect from corrosion [ATTACH=CONFIG]96587[/ATTACH] Here is the seat all back together, its much better than before and a lot easier than I was expecting.
-
I have offered up the centre console plastic from my old dash and it seems to fit ok, and all the buttons in the centre attach to this plastic. I already have the spoiler button in which fits perfectly. The only one I have yet to try is the headlight switch. My car also has early leather seats so I guess mine is turning into a bit of a crossover.
-
A couple of weeks ago I bought a black dashboard from an early car, for the price I paid it was worth a shot to see if I could make it work with all the bits from my late dash. I have read that the only difference is the metal frame, the late dash is deeper to accommodate the deeper storage compartment. From doing a bit of reading I have seem people suggesting drilling out the spot welds on that part of the frame but that seemed like too much messing about. After spending some time comparing the 2 dashboards side by side it seemed obvious to me that the metal frame is removable and almost identical between the 2 dashboards apart from the centre section. [ATTACH=CONFIG]96482[/ATTACH] The frame is attached using some weird 9mm nuts and a few rivets. [ATTACH=CONFIG]96480[/ATTACH] You can see circled in the above image the difference in the 2 frames. The late dash is the longer one at the top. [ATTACH=CONFIG]96478[/ATTACH] Here is the late metal frame in my early dash, I put some silicone sealant between the frame and the dash to maybe help with rattles and creaks in the future. [ATTACH=CONFIG]96476[/ATTACH] I used new rivets where the old rivets were, I will paint any that are on show black at a later time. [ATTACH=CONFIG]96474[/ATTACH] I test fitted the dash in the car and it seems to fit perfectly, I just need to paint my demister vents and speaker grills as well as refit all of the HVAC pipes and the dash can be installed for good.
-
Thanks but I got myself a rent free bottle from Adams gas at the weekend, what I actually needed was the regulator and a hose adaptor for my welder. I now have everything I need to start welding again.
-
So while i'm still working on getting a better gas system for my welder I thought i'd get on with the interior. A couple of weeks ago I bought a black dashboard from an early car, for the price I paid it was worth a shot to see if I could make it work with all the bits from my late dash. I have read that the only difference is the metal frame, the late dash is deeper to accommodate the deeper storage compartment. From doing a bit of reading I have seem people suggesting drilling out the spot welds on that part of the frame but that seemed like too much messing about. After spending some time comparing the 2 dashboards side by side it seemed obvious to me that the metal frame is removable and almost identical between the 2 dashboards apart from the centre section. [ATTACH=CONFIG]96446[/ATTACH] The frame is attached using some weird 9mm nuts and a few rivets. [ATTACH=CONFIG]96448[/ATTACH] You can see circled in the above image the difference in the 2 frames. The late dash is the longer one at the top. [ATTACH=CONFIG]96450[/ATTACH] Here is the late metal frame in my early dash, I put some silicone sealant between the frame and the dash to maybe help with rattles and creaks in the future. [ATTACH=CONFIG]96452[/ATTACH] I used new rivets where the old rivets were, I will paint any that are on show black at a later time. [ATTACH=CONFIG]96454[/ATTACH] I test fitted the dash in the car and it seems to fit perfectly, I just need to paint my demister vents and speaker grills as well as refit all of the HVAC pipes and the dash can be installed for good.
-
I ran out of gas again for my welder. Currently i'm using the small disposable C02 Argon bottles but they don't last very long at all and at £12 it adds up quickly. I have been looking into converting to a larger bottle but i think more research is needed first. While I am out of gas I decided to paint the passenger side inner wing, it may be a bit early for this so I will have to try and protect it in the meantime but I think it looks pretty good. [ATTACH=CONFIG]96300[/ATTACH]
-
[ATTACH=CONFIG]96222[/ATTACH] I primed up the whole area around the battery bracket and tried some of the Dragon Green pearl paint from Halfords, the photo shows 1 coat which was maybe a little too heavy (try to ignore the runs). At the time of the photo the paint was still wet and the light was shining directly onto the new paint, The match isn't too bad but not perfect either, the old paint is darker but I hope once another coat is applied the match will be much closer. Another issue would be that the original paint is very old and tatty in the engine bay so that doesn't help the match. Im not too worried anyway as there is a lot going off in the engine bay to break up any slightly mis-matching colours, i probably wouldn't use the Halfords paint in the middle of an outer panel. [ATTACH=CONFIG]96224[/ATTACH] I gave the wheel arches a clean and they actually clean up nicely with the original paint largely intact. It looks like one of the previous owners had wheels big or wide enough to rub. I also managed to source some front wheel arch liners that will hopefully stop so much muck gathering up behind the wing. [ATTACH=CONFIG]96226[/ATTACH] I started cutting out the rust on the front of the passenger sill. From this I ended up working my way back straightening the sill and stripping off the loose underseal. [ATTACH=CONFIG]96228[/ATTACH] This is a patch of rust that I cut out further back in the passenger sill, it spans across the sill seam however the middle sheet seems largely unaffected. I cut out the metal on both sides of the sill and rust treated the center sheet. [ATTACH=CONFIG]96230[/ATTACH] I have started cleaning up all the muck for the while engine bay, this is the drivers side inner wing area before I began cleaning. I will take some pictures of the cleaned engine bay at a later date however this is what the drivers side used to look like as well.
-
I decided to tackle my first rust hole. The battery tray seemed to be the easiest to tackle first. I drilled out the original spot welds for the battery bracket to reveal the extent of the rust. [ATTACH=CONFIG]96080[/ATTACH] I started by cutting the thin and rusty metal out as well as cleaning up other areas of surface rust. [ATTACH=CONFIG]96083[/ATTACH] I used zinc galvanising spray to cover up the bare metal, mainly for under the bracket to protect it from further rust once it is welded back in place. Zinc galvanising spray is weldable. [ATTACH=CONFIG]96086[/ATTACH] This is the new metal welded in place, anyone can look like a good welder if they can use a grinder. I did go over the bare metal in zinc spray after the image was taken. [ATTACH=CONFIG]96089[/ATTACH] [ATTACH=CONFIG]96092[/ATTACH] Here is the bracket spot welded back in place. I have test fitted the battery and it bolts down well.
-
I want to start trying to run my freshly wrapped loom in its final position but I thought id better give the panels a bit of a clean because they are caked on with oil and muck. [ATTACH=CONFIG]95963[/ATTACH] I started with the battery tray area, it was covered in a layer of dirt, which covered a layer of oil and grease, which covered patches of dried waxoyl. Nothing i had seemed to shift the waxoyl very quickly, white spirit and elbow grease seemed to be the only thing that worked but it still took a while. I think I probably spent an hour on this small section. Most of the rust is surface rust from scratches but as you can see there is one small rust hole next to the battery bracket that will need to be repaired. I think i'm going to have to drill out the spot welds for the battery bracket to get full access to the rust area. Once the hole is repaired I will probably just scuff up the area, remove surface rust and rattle can the area. Once the car is back together this area isn't very visible anyway. Halfords seem to do the correct paint code in their aerosols for £5.94 with a trade card which seems good value. [ATTACH=CONFIG]95969[/ATTACH] [ATTACH=CONFIG]95972[/ATTACH] After getting bored with cleaning i went back to wiring. Previously I had created a temporary relay loom to take power for the headlights directly from the battery. This was done with wired running directly to where they were needed using the only wire I had on hand, this made a functional but terrible looking mess. I always had the intention of tidying it up and now is the best time. I cut off the old crimps and crimped in new (plastic insulated and higher amp) wire and crimped using my new and much better ratchet crimps. [ATTACH=CONFIG]95975[/ATTACH] I used 3 relays in total, one for low beams, one for high beams and one for the fog lights. I never wired up the fogs before so I don't know if it will even benefit the fogs but I figured it couldn't hurt. I ran the wires around the loom that I put up in the scuttle to help keep it out of the way. I will tape the headlight loom separately for 2 reasons, 1 to keep my loom separated from the original loom, 2 because I already wrapped the original loom and I wasn't going to unwrap it again. [ATTACH=CONFIG]95966[/ATTACH] Jumping back into the car, I started to put the fuse box back together. I found that there is nowhere near enough room to fit all the wired behind the fuse box, I now understand why the fuse box was always hanging with the fuses facing downwards. The only reason i can think that its such a mess is due to the Clifford alarm system, as far as I can tell the 20v wiring is all in the engine way apart from a few that come through. I did my best at tidying it all up but inevitably in the wrapping I did trap a few wires luckily as you can see in the photo it seems to be just 2 ground wires that don't reach the earth post. I will probably just extend these rather than pulling everything back out.
-
I haven't seen any other rust holes but it would definitely be worth checking, do you mean in the scuttle panel area? I really want to be able to drive it this summer so I'm going to concentrate on the engine and drivetrain parts to get it driving well. The rest can be done in my own time while still been able to drive it.
-
Thanks for the positive comments. Ive been working of the car most of today and I think I have made some good progress. I'm mainly working on getting the loom sorted out, that involves: - pulling the old crusty tape off the wires - making sure that there is no damage to any of the wires - determining if there is any way of optimising the wiring loom route - determining the length needed for any branches for optimised loom routes - re-tape the loom [ATTACH=CONFIG]95849[/ATTACH] You can see in the above image the tape is crusty and just falling off, this wire is likely part of the original Corrado loom. [ATTACH=CONFIG]95855[/ATTACH] I decided to try and put wires up in the scuttle area where possible, I have a one piece scuttle panel so there is lots of room and is protected. Somehow I will have to try and get a rubber bung to fit this hole, I don't remember what actually went up here and whether there is already a bung somewhere. Does anyone know what this hole is actually for? [ATTACH=CONFIG]95858[/ATTACH] Here's the loom up in the scuttle. [ATTACH=CONFIG]95861[/ATTACH] Here's the loom coming back into the engine bay on the passenger side. [ATTACH=CONFIG]95864[/ATTACH] I also got the passenger wing off, I already knew about a rust hole at the front of the sill so this was to prepare for the repair. Judging by the amount of dirt I think I need to invest in some arch liners. [ATTACH=CONFIG]95867[/ATTACH] Here you can see my hole, this is after prodding and pulling at the metal surrounding it so I don't think I will have to cut much more out. Looks to me like its definitely worth pulling off the other wing as well to clean everything up and check for anymore rust, then probably a healthy coating of under seal on everything not visible. There is a few areas of surface rust in the engine bay that will get cleaned up, this means either trying to colour match the best I can or using some kind of durable black paint that will hide any imperfections in the paint job.
-
I figured I would create this if nothing else as a place to document my build progress. If anyone actually looks at this then I guess that's a bonus. I must also note that I have never posted a build thread on any forum before. I am also not a mechanic, i'm just an enthusiast keen to learn with the help of more experienced friends. [ATTACH=CONFIG]95825[/ATTACH] I bought this last year already converted to an AGU 20v 1.8t engine fully working and driving. I was using it regularly on the weekends but I became increasingly annoyed at the engine bay with its mess of wiring, caked on dirt and grime everywhere and most importantly the failing turbo seals causing plumes of smoke at idle. After purchasing my first house with a suitably sized garage I decided it was time to pull the car to bits to tidy up everything and fix anything worth fixing while I was in there. [ATTACH=CONFIG]95831[/ATTACH] The above photo is just before the car went in for the final time for a while. [ATTACH=CONFIG]95834[/ATTACH] With help we managed to get the engine out onto the crane in 2 and a half hours which doesn't seem too bad. All bolts and fixings bagged up and labelled as well as all electrical plugs taped up and labelled. [ATTACH=CONFIG]95837[/ATTACH] In order to access the wiring in its entirety the dashboard needed to be removed, this is where I found even more wiring mess that was all tangled up and several wiring looms spliced into. The splicing on the whole was actually done well but the car is fitted with a Clifford alarm in which the splicing seems questionable in places. I will keep posting images and information as I work through the car.
-
Right I have progress. I have spoken to a friend at VW who has pointed me in the right direction which may help others, although I guess it is a weird problem to have. Like vw rule said there is a large "sleeve" that sits inside the plastic switch housing that has a pointer sticking out the top. He sent me this diagram and part number. [ATTACH=CONFIG]95091[/ATTACH] [ATTACH=CONFIG]95092[/ATTACH] I think this is the workshop manual diagram which seems a lot better. [ATTACH=CONFIG]95094[/ATTACH] I found an image of the part here [ATTACH=CONFIG]95093[/ATTACH] From VW its costing me £13 for the new sleeve but is on back order. Hope this helps someone else too.
-
Thanks for the detailed reply. I have looked at the video and it seems like there is something other than a standard washer between the top nut and the linkage, maybe that has an arm that pushes on the switch? its difficult to tell from that diagram but it doesn't appear to show any kind of arm. Im not sure why the sleeve bearing is relevant as I assume they are there to hold the linkage in place as it moves up and down the shaft? I have found another video that shows the mechanism for a newer mk4 golf which looks very similar and I have attached an image of that.[ATTACH=CONFIG]95090[/ATTACH]
-
I have fairly recently purchased my Corrado and the reverse lights never worked. I did some digging and found that that switch works perfectly when pressed and the reverse lights lit up. However there is nothing on the linkage that would press on the switch to activate the lights. Could anyone take a photo of the mechanism that presses on the switch so I can buy or try to fabricate something. Thanks. [ATTACH=CONFIG]95087[/ATTACH]