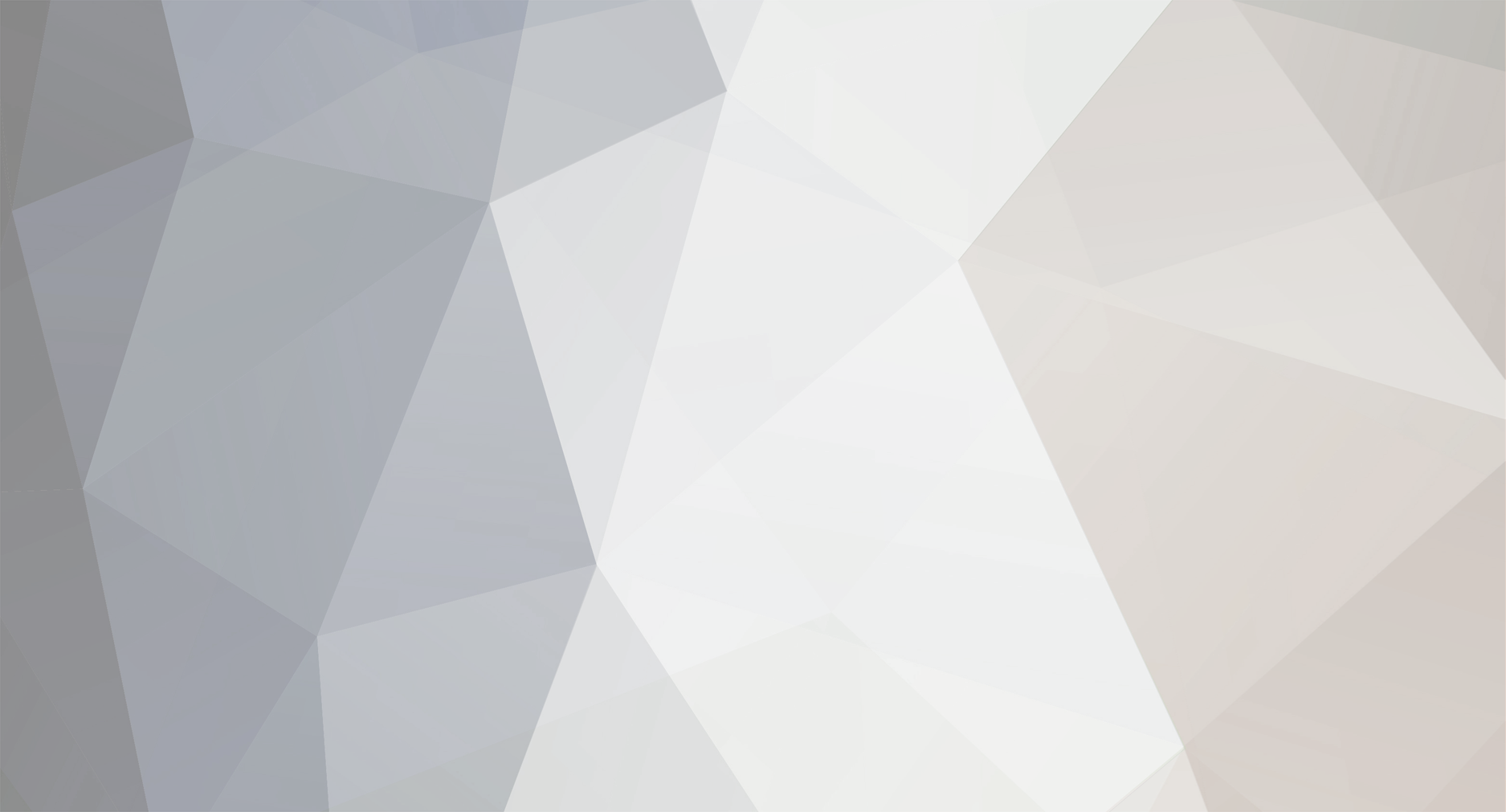
Albie
Members-
Content Count
73 -
Joined
Content Type
Profiles
Forums
Blogs
Calendar
Articles
Gallery
Downloads
Store
Everything posted by Albie
-
Can anyone advise on a strange condition of my ABS on my 2.0L 16V? The ABS has never given a hint of trouble in 2 years. Forgot to turn off the sidelights yesterday and in the evening the battery was flat. When I tried to start it, it turned a few times but gave up the ghost as it would do. However, the electrics went into a strange condition where the indicators for both sides, the ABS warning light, and the dashboard security alarm LED all turned on and I couldn't get them to turn off. When I restarted the car with a jump from my wife's Golf, (which was easy at the first turn of the switch), I let it run to charge it for a couple of minutes, stopped the engine, reset the alarm, the indicators reset themselves, but the ABS warning light will now not turn off. When I start the engine it gives a little flicker as it used to but then stabilises and stays on. The brakes seem fine, the fluid is full to the top mark still, but nothing I do will turn off the dashboard warning light. Can anyone suggest what is wrong?
-
Dunno if this will help at all but the ISV seems to have an action which is not quite obvious. It is under the control of the ECU of course, and it is basically an electromagnet pulling its iron core in against a spring of known strength. But is isn't fed a varying DC voltage to set the tickover. The ECU is a digital device and I'm pretty sure will feed the valve pulses which the valve then averages out. If that is correct and you try to read the voltage level at the valve plug while it is in action with a simple meter you will get meaningless results. What you are reading with a DC meter is a stream of fast pulses and not a DC voltage! One contact should read +12V supply with the plug disconnected and the other, the effective ground is under the control of the ECU. The only way to really check its action would be to stick an oscilloscope on it and look at the pulse stream to see if that is reacting correctly. Or use the right analytical software of course.
-
I've just had this same problem myself on my standard 2.0L 16V. Previous dork had the leads just pushed into new pins of the ISV plug and not even crimped down. I found out when they slipped out with no way of knowing which they had come out of. It looks like there is no right or wrong at least on my machine's ISV. The valve is basically an electromagnet with a coil which pulls in a central iron core against a calibrated spring. I posted for advice and got some help but we couldn't come up with anything conclusive, so I just put it back together without looking and it seems fine since. I'd give it a while for anyone more experienced to offer better advice, but I can't see it being relevant.
-
Durhhh! Yep I found it. In amongst a lot of links to discussion about 16V ISV problems I had come across this post on VWVortex. I didn't notice it was relevant to the CIS-E setup which does apparently have the ISV and screw adjustment. Sorry, latest in a string of senior moments. http://forums.vwvortex.com/zerothread?id=3462207 Does make you wonder if a throttle body swap of some kind to one with screw adjustment isn't possible though, to reduce total dependence on the ISV. It may be a non-issue but it might just be interesting. Anyone any thoughts?
-
I wonder if I have cut in on a discussion about a different model, Audi maybe, and just assumed that because I recognised things they were talking about the Corrado? It could be, but the gist of the info was exactly as I described. "Why not do away with the ISV and rely on the screw adjustment solely like I do". It was even reported that it is a bit more difficult to do this in winter as the screw adjustment is not so temperature independent as the ISV. If I can retrace my steps I'll post a link.
-
I know the Scirocco has no ISV system and is completely manual on the screw. But I have read of Corrados with both an ISV and an adjusting screw. It is often advised to do away with the ISV and run only on the screw, particularly on American sites. This seems to me to maybe give the best of both worlds. My current problem is with a tickover which is fine for a while then drops, falters and dies rather than runs high. As I understand it, the screw isn't there to set the tickover to its working level, it is to set it to a kind of lower minimum default level. The system I mentioned kind of sets 2 effective tickover levels, a working one and a sort of backup one which you hope you'll never need. Let's say the ECU wanrts to set the ISV to allow tickover at 950rpm. You disconnect the ISV and adjust the throttle screw to give a tickover of around let's say 800-850rpm. When you connect up the ISV again it will take over and adjust the tickover back up to 950rpm of course. If it ever gets into a stew and loses its ability to control for whatever reason it will stop passing as much air but the manual backup means the level cannot fall below 850ish, even with the ISV completely out of action and closed. There should be no problem with the ECU asking the valve to add just a little air to the intake to up it from 850 to 950 rather than the full quota needed to tickover, it's a continuous feedback system and is continuously self-compensating. At the moment without the manual system, if the ISV or its ECU control fails then I am shafted! Some would say that the ISV only system is more sophisticated. Some cynics may say it forces you to buy another very expensive component when it fails in order to get your Corrado back on the road! ;-) Have you ever looked at how little is inside an ISV and how undemanding the construction is?
-
I have had another try to make sense of the schematics posted on the Russki VW site. I can't find any reference to wiring for the 9A engine. (so what's new), only to what seem to be the 4 cylinder SOHC and the VR6 models. For all of them the ISV, or the Idle Air Control Valve as they call it, is labelled with different colours but with no pin numbers associated with the plug at the valve end. I think we must be able to assume that it makes no difference which way round they are connected, otherwise they would surely have numbered them wouldn't they?
-
Thanks for the feedback Nocrap. The colours are a little confusing though. My colours are definitely Blue base with thin White stripe, and White base with thin Black stripe. I would think that when you sat White you are referring to my White with Black stripe, and my Blue with White stripe is your Black. You can't confirm which is the +12V when the ignition is on can you, then we can do away with any need for colours?
-
Just found the last bodger has fitted a new plug for the ISV without crimping down the connectors properly. After a history of occasional tickover problems I actually heard a slight crackling as I bent the cable near the plug. When I investigated the darned things just slipped out! The plug is numbered 025 906 231 but I have found out this may be superceded to 443 906 232 on other setups. The ISV is numbered 048 133 455. I have the 2 crimp pins out of the plug without any damage and I have borrowed a good crimp tool from work to fit them properly. Now I need to know which terminal is which? (The picture below is not my own plug, mine is in much better condition than this.) 2.8l 24v Climatronic system.pdfISV AMP Plug.jpg[/attachment:1y4ty0a1] The plug has a "1" and "2" moulded into the body at the cable entry point behind. Plug Nos.jpg[/attachment:1y4ty0a1] You can see the numbering of the terminals in these plugs. In the first picture pin "1" is on the Right. On mine, wires to it are coloured Blue/White and White/Black. Logic tells me that as the ISV is basically a coil electromagnet pulling a metal plunger against a spring it shouldn't make any difference which wire goes to which. But experience tells me to get it right! I believe +12V is fed through one wire and the ECU controls grounding via the other wire so it could be relevant. Can someone please tell me which way round the wires should be fitted. It would be enough to know that +12V should go to pin 2 say, as I can of course identify which wire is my +12V and take it from there. One other thing which I find strange is that I have absolutely no idle adjustment on my throttle housing. There is no adjusting screw coming out towards the front of the car bleeding a little air past the smaller butterfly, or anywhere else for that matter. (I have run a few Sciroccos so I am familiar with this system). Common folklore seems to say that I should be able to set a slightly low tickover with the screw and the ISV takes care of the rest. Can anyone explain or am I thinking of something else?
-
Can someone elaborate a little on the ECU vacuum pipe having to be exactly 1m x 3.5mm? I have never heard of this. Presumably the volume in it is critical to correct ECU operation?
-
Thanks David. That was much what I expected you would say. Guess it means a trip to the local dealer for a new 12 point stretch bolt as the others seem to be getting as rare as hen's teeth.
-
There has been much discussion about crankshaft pulley bolts for the 2.0L 16V 9A engine before. Some prefer the newer 12 star point stretch bolt and some the older reusable hex bolt and washer. One useful point I can toss in here is that the setting for the stretch bolt has been causing some confusion. I have seen it quoted in posts as being 66ft lb/90Nm + either 90deg or 180deg. I knew I had seen it as both in reference literature too as I had it wrong in my head. I got to the bottom of it the other day when I found a reference which showed that the 180deg final setting was for the 8V PG type engine, even though the diagram is very similar to the 9A!. So for the 9A, 90deg is the correct final torque, (thanks to Crasher for the timely warning, you were spot on again! I couldn't rest until I knew where I had seen that 180deg.) So now to the important question, can anyone tell me whether the reusable M14 type hex head bolt on the KR 16V is the same as the bolt from a 1.8L 8V Scirocco GTX? (That is NOT the 16V, it's a B reg 8V). My guess is the Scirocco is smaller but I just wanted to rule it out for definite.
-
Looks very like a large wirewound power resistor to me. No idea if it is anything to do with the ABS though. Unless you can see the leads linking up directly with the ABS it could very well be something to do with another system just mounted there because it was handy. Have a close look at it and look for any tiny burnt spots on the coil of resistance wire. When these go it is usually a weak spot having overheated and burnt through. This can be just the size of a pinhead at one spot on the wire coil. One tiny break and the whole thing is kaput.
-
What level of fuel did you have in the tank at the time? How old is your lift pump in the tank? If the outer main pump is suddenly noisy it could be being starved of fuel which could point to the lift pump not supplying it with enough to keep the reservoir full.
-
I'm building up the engine after a particularly long rebuild and have just found something peculiar. The spark sensor which should be wrapped around the number 4 cylinder according to my PDFs is actually around number 1 lead. And to match that, the plugs are 180deg out on the distributor cap. These 2 may cancel each other out of course on an engine incorrectly but accurately timed up that way. There must have been something peculiar about the original arrangement which I didn't even notice as I stripped it. Having now timed things up correctly, everything is going back where it should be, so the leads are being swapped 180deg to match the rotor arm, but is there any need to take the spark sensor off lead 1 and put it onto lead 4? Having done one of these before, I know it can be a bit of a bitch to do. If it just senses a spark which it then counts for things like the rev counter it should be fine, but if it is timing things relative to cylinder 4 then it could seriously screw things up. Any advice from you guys who know?
-
Thanks Easypops. I guess the Corrado is a different beast after all. Shows the value of the forum doesn't it, 18 to 30 is a bit of a jump to get wrong! 30lb ft/40Nm it is and thanks.
-
I think I may have answered my own question and found it didn't need asking after Easypops' post! I have managed to find the setting for the 1.8L 16V Golf online. It's not a Corrado but can't be too different. That seems to be 18ftlbs/25Nm too. I guess that was what Easypops meant in his last post. If no one says different I will have to assume that this is correct and the head/manifold and manifold/downpipes are both set to the same 18ftlbs 25Nm.
-
Duhh! I have that doc available too, and I never noticed they were there. Thanks Easypops. Another "Senior Moment" comes and goes! Anything on the manifold to downpipe nuts? (They aren't there as well are they? :oops: )
-
Can anyone advise on torque settings for the 6 manifold to downpipe nuts, and the 8 manifold to head nuts on a 2.0L 16V 9A? Can't seem to find them anywhere. Thanks.
-
Just resurrecting this idea as I am sure everyone who was initially so helpful has assumed I have just forgotten it. Sorry to have been out of touch for so long but work sent me abroad for weeks and an overseas holiday also got in the way. So I have had a good period away from internet access. I haven't dropped the search, I just haven't had much time to collate everything and put it into a document for checking. Supercharged very kindly gave me access to a lot of info but none of it is absolutely specific to the 2.0L 16V Corrado, just the 9A engine as used in the Passat, so I'm sifting it very carefully before assuming things are the same. And I have only managed to find some of the settings for ancillary stuff in a Corrado general 4 cylinder source. I'm working on it now and hope to have it finished in the not too distant future, (work permitting). In the meantime I will soon be posting a list of settings I haven't been able to find yet which should round the info off. Thanks for your patience.
-
Just to round off here. I used a couple of exhaust manifold to downpipe nuts as spacers over the new bolts and wound them in with their own old nuts. I made sure to use a torque wrench set to 22lb, the first stage in the tightening sequence, so I could check that they didn't go over and begin to stretch at any time. It was a piece of proverbial and in about 10 minutes they were all in and I could finish the bottom end. Thanks for the advice.
-
Thanks once again for the advice Veedubbed. It is really just a case of worrying about whether this is the normal state of affairs or whether there is something really wrong. I have done this job many times before, but never with stretch bolts in this location, so I'm used to these bolts only needing a mild push home or going in far enough to use the cap to finish the job as they are tightened home. If they are normally this tight, winding them in seemed to me to be a sensible thing to do. I was worried as to whether this would need so much pressure that the bolts actually stretched, knowing that this is what they were made to do. Now you have confirmed it isn't too unusual, I'll find something to use as a sleeve and try pulling them in using one of the old nuts.
-
I'm rebuilding the bottom end of the 9A and putting in new big end bolts like a good boy. They look exactly the same as the ones I have taken out but I can't get the new ones into the conrods. I don't mean just the knurled final bit just beneath the head, I mean the two stepped shoulders just after the thread. That doesn't give me any thread poking through the bearing cap to wind them home with the new nut. So can someone tell me just how tight these should be and, assuming these are right, what is the best way to get them in?
-
That's more great info Crasher. Thanks for your help. I will start pulling things together for the Wiki in a day or two and we can get you to check over the finished info. It looks as though the best way of getting it into the Wiki proper will be through the moderators, so the document you check will be the finished one that gets submitted. That seems safest, (in other words I can't make any further mistakes if I don't edit anything after that point.) I hadn't thought of including part numbers but that is a great idea where we can. I don't know whether people like yourself who are experienced with the 9A will be able to access the Wiki doc and add more info directly, but it would be useful if you could. That way it takes away the problem of having more info constantly dribbling in needing to be included, and having to bother moderators all the time, (I'm sure one or two actually have lives to get on with!)
-
Absolutely right Crasher, we must have accuracy. But aren't you missing the point whereby posting the settings in this thread first was meant to sort out any inaccuracies before posting it in the Wiki! I could have just started entering directly into a Wiki page and let it grow there but I share your desire to keep things right. Thanks for your input, it is clearly needed to keep everything correct. Easypops posted his 2 documents which gave a great listing of most of the values needed. His doc clearly shows 40Nm and 60Nm, it's completely my mistake in listing them here as 40 and 60 lb ft, but it is a typo and not in any way a finished form. But that just proves how much we need others like yourself to check things out and clear them, and nothing will be finally entered until it has been fully cleared. Also, there is the ability of other members to edit and clarify anything which ends up on the Wiki. So that's one major correction and a useful piece of additional information about the head bolts which we now have. Maybe I could send you a final draft to proof read when we reach an end point, I would appreciate someone taking on that job. Just a careful read through of the list and a nod of the head would be sufficient. Thanks. Now in the interests of increasing that same accuracy, we can differentiate between those smooth and ridged head bolts. Smooth non-ridged bolts are for composite and those with ridges round the edge are for metal gaskets? I know there are some which take washers and some which do not, where do they come in the picture?