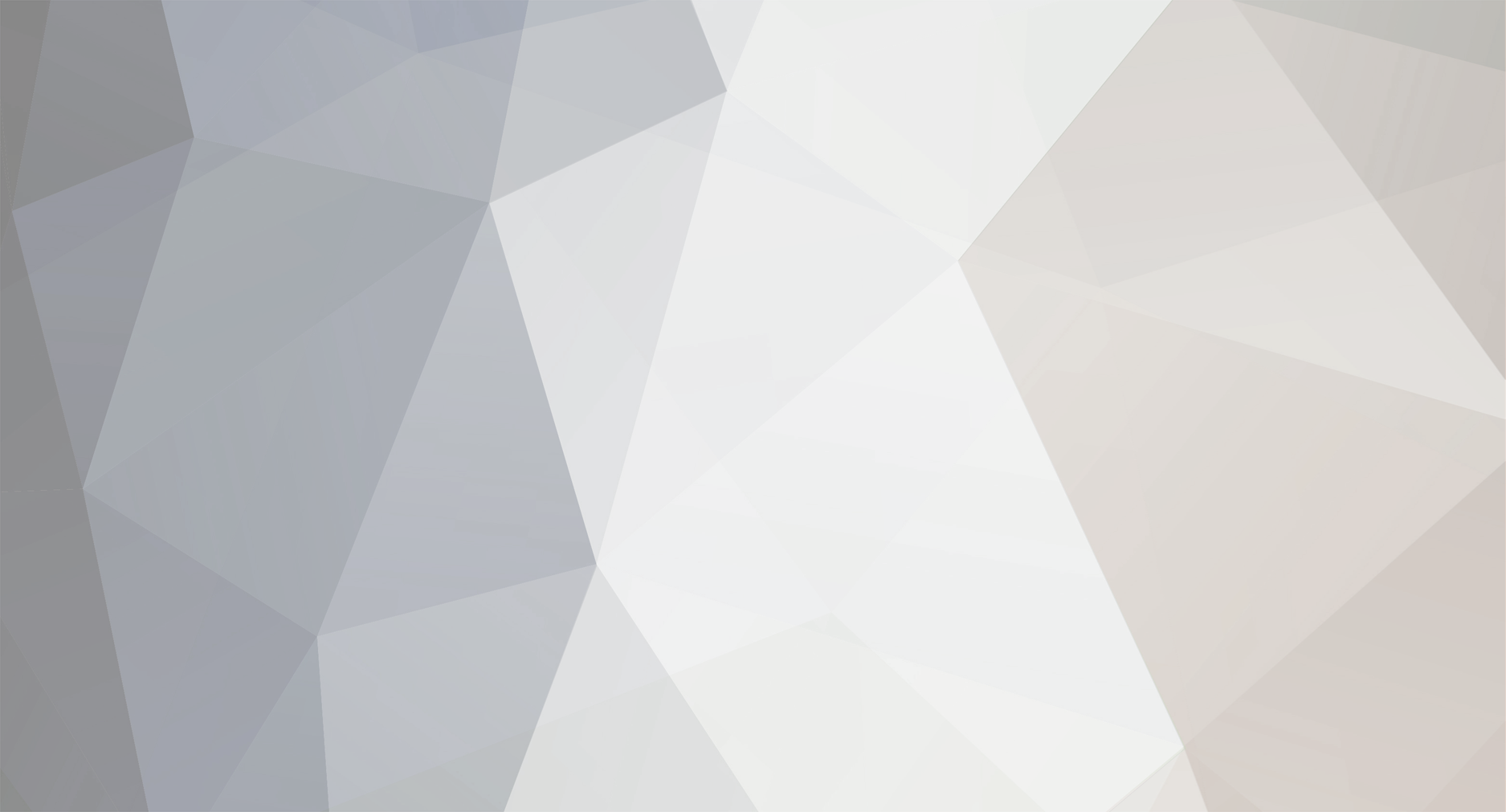
Bazmcc
Members-
Content Count
245 -
Joined
-
Last visited
Content Type
Profiles
Forums
Blogs
Calendar
Articles
Gallery
Downloads
Store
Everything posted by Bazmcc
-
Don't quote me on this but I think the rear outside leg sits 3/4" too far out. Because I think the rear rails are the same width as a mk4. That's just from memory. Easily sorted with a ginder and a welder though.
-
Sounds good. Make sure you take some pics when you get it fitted.
-
Helicoils are added complexity too though as it has to be drilled out wider meaning the walls are weaker. Making it from steel is another option as it's only a small part but something like 6061 T6 shouldn't strip if the threads are well cut but the smaller the threads the easier they are to rip out.
-
The only issue I can see there is the grub screw? It'll probably work perfectly fine in most cases though. There will be a percentage of people who might ring the threads out of it though. What grade of aluminium did you use? A good way to stabilise that would be to put a countersink into the tab on the bracket about 1mm deep to let the grub center on. It's not a million miles away from what I've drawn up. I'll try and get it sorted as soon as I can?
-
Exactly. Don't worry I haven't forgotten about this. I have a design drawn up rough so I'll get it done accurately next week and we'll cut up some metal.
-
Definitely Poorboys Natural Look. We sell loads of it at shows.
-
In theory it should look quite like a standard MK4 one as it'll be covered by the gaitor. The hardest part is getting the main radio cage fitted in well with the center console trim that fits over the tunnel. Hopefully I'll get a gaitor soon if I remember and get it test fitted. Now I know what needs to be done I should be able to finish it fairly easily.
-
OK so got back to a bit of work on this last night. First thing I needed to do was extend a couple of wires for the lights from behind the dash so I could work on them. I also shortened the wiring to the radio, diagnostics socket, glovebox light, and center console fuel flap switch. I wanted to get all this done before putting the dash back in for testing the shifter box and mechanism. Here's another little thing I noticed and needed to be corrected. As the groove for the spring had been recut 12mm down and I'm using the MK4 plastic pivot in the middle I had to recut the groove a bit longer so I could press the shifter down to get into reverse. I extended the groove from 23mm up to around 33mm up towards the top. Then put it all back together to get it into the car to see how it fitted. It now has a decent margin of clearance but i'm concerned about the center console clearance around the gaitor when it's in 2nd, and 4th gears so i'm going to put two 45 degree bends in the flat steel so it'll step up and back higher and towards the back. That means the back of the flat steel won't be as close to the console or end of the handbrake. I also decided to mock up the doorcards again to check for clearance. I had to trim a little out of them but they should fit fine. I'll be making a fibreglass flat panel for the part I've cut away that should fit on the door and be covered by the dash. I'll retrim it in the same material as the rest of the doorcard when I get round to it.
-
Still working on the MK4 dash among other things. http://the-corrado.net/showthread.php?66329-The-MK4-Golf-Bora-Dash-Conversion/ And the seats. http://the-corrado.net/showthread.php?74537-How-would-these-aftermarket-seats-look-in-a-corrado
-
I need a dust boot for my slave cylinder so if you have an old slave cylinder with a good dust boot on it, I'll gladly take it off your hands. Let me know. Thanks Baz
-
Every cut, drill, grind and bolt is in this thread. Pages 2-5 is what you need to read through.
-
You've just tempted fate. Lol.
-
I think we have a decent solution now. I'll make it out of plastic at the start of the week if I get a chance. My mate said to call in with him as soon as I have a mock up or even measurements and a drawing and he'd cut it out on the mill. This should be able to be fitted without even taking the cable or bracket off the car. I'll update as soon as we have something I can show you all.
-
Was working on wiring for a customer today so didn't get as much done as I'd like. Called up with the engineer and he gave me the shifter and a piece of flat steel for test fitting. So, Corrado shifter rod and bracket, MK4 plastic and spring, Corrado clip, Flat Steel, and MK4 shifter rod top half. This is just a test piece. The real one will have a thicker piece of plate in the middle. This one is about 5mm. We'll be going for about 8mm plate for the final version. We machined the top half off the rado shifter, fitted the MK4 plastic bracket in the middle and as it was shorter we cut the groove for the clip about 12mm (I think) further down the shaft. Then we refitted the spring and took a step off the top of the shaft to fit the flat plate onto. The narrowed part is 9mm. Snug fit. And the finished thing will be something similar to this but we'll confirm how far back the step is when it's test fitted. I'm not sure if it'll go straight up or if it'll be angled as shown. This depends on clearance from the radio cage.
-
There's a couple of issues I've spotted with the gruven one which isn't ideal. The way it fixes to the bracket isn't very good so we'll avoid that. As far as I'm aware it's a stepped slot where the cable surround goes in and the cable itself fits through the end.
-
Ok I think I have a design that will work well (the eureka moment). I need to take my bracket off and make a few measurements and then i'll put it into featurecam or else solidworks. Main criteria. It has to be modular so it can be easily removed or have parts replaced. No modifications will need to be made to the existing bracket. No modifications will need to be made to the existing cable. No welding or drilling will be required. There will be no sprung parts as they ultimately lead to fatique failure.
-
Tubes fitted.
-
The idea will be something like that hopefully. But without the cable ties maybe.
-
I have the engineer on standby with a CNC mill and lathe and we're going to have a go at coming up with a solution to the crappy excuse for a clip on the bonnet pull where the cable attaches to the bracket. This is the standard clip both normal and broken. The gruven one looks like it does the job but involves drilling holes and i'm not sure i'm convinced by the design. Gruven make this one: So I'm going to try to come up with a very basic and easy to fit version. Any pics, suggestions or help is greatly appreciated. We might as well make a solution for it because it seems to be an all too common problem.
-
If you want I can get you some pics of what way the stud on my floor is set up as I have my dash out at the minute.
-
Tubes for the handbrake cables. I'll show these fitted as soon as I get a chance to put them in.
-
Here's how I found my slave was done. I unbolted the 13mm bolts, slid out the slave cylinder and as I lifted it up slightly the pin fell out accompanied by about a spoonful of fluid. It was fairly obvious then. To check the Master get your head under the dash and try and feel up below where the pin goes through the firewall into the master and if you can feel fluid it's probably leaking past the seal there.
-
Has anyone got an old slave cylinder laying around with a good dust boot?
-
I'd say the slave seal has gone. By the way, if your dust boot in the slave cylinder is still in 1 piece I'll buy it off you. I have an almost new slave in mine and I need a dust boot.
-
Happy new year everyone. I'm starting to realise how long this conversion is taking but I think it'll be worth it. My engineer has been off for the xmas and new year hols so I haven't be able to get the gear shifter and handbrake finished yet but it'll not take too long to sort when he gets back on it. Currently I still haven't been able to get the wiring all sussed out because I've been working on loads of other stuff in the mean time. The airbox ducting adapter is almost finished. A couple of coats of paint and it'll be done. I need to shorten a couple of bits of the wiring loom just to tidy it up a bit as they are very long. But other than that, things are moving slow, but still in the right direction. The reason I've been dragging my heels is that i'll basically be trying to eliminate the rado original fuse box as much as I can. So the wiring diagrams keep getting bigger. Stay tuned. I'll update soon. I'll be using MK4 10 pin headlight connectors to join the looms together.