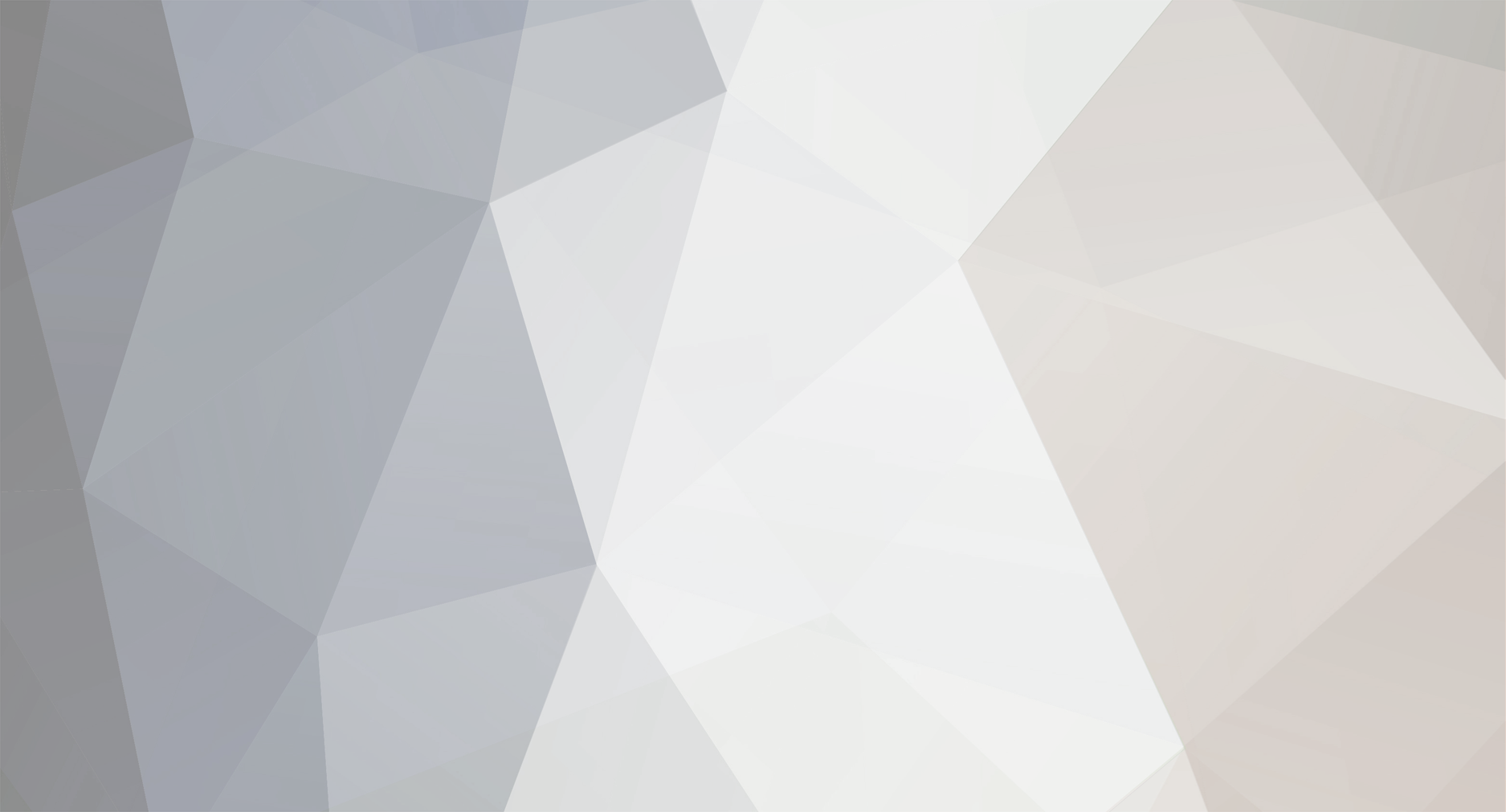
just_say_meth
Members-
Content Count
393 -
Joined
Content Type
Profiles
Forums
Blogs
Calendar
Articles
Gallery
Downloads
Store
Everything posted by just_say_meth
-
Anyone got any good ones? Not really after ones of the car, more the engine and charger as a whole. Found a good one in my Brooklands Book but a little bit small. TIA Andy
-
Smooth bumper how-to
just_say_meth replied to just_say_meth's topic in [Archive] Wiki Submissions & Collaboration
Aye it makes sense mate, I actually bought one but have never used it :lol: The only thing I can think of that wouldn't work is the rolls/sticks of plastic that you can buy don't match the bumper plastics. From doing various bumpers I''ve found if you don't use the same plastic throughout then it doesn't hold. However you could easily make up your own sticks from a donor bumper and feed them into the nozzle, will need to give it a bash :norty: Cheers mate, have you tried it out yet? pop some pics up if you can :salute: Sorry to everyone waiting on the rear bumper, have started a new job and have had very little time to do anything. I will try and get it sorted soon though. Finished the TT bumper and it looks awesome. Spoke to a few TT guys at various shows and apparently it's a difficult bumper to weld. Next up the front plate recess on my S4 :norty: Link to the TT bumper: http://s170.photobucket.com/albums/u242 ... bumper/TT/ After I finished it, it was prepped and painted and how now been wrapped in white vinyl, I'll get some photos of it on the car tonight :wink: -
Sucks this has happened mate, your having about as much luck with your Corrado as me :lol: I'll have to pop over and help you get this sorted, how you fixed for sunday, might be able to nip through?
-
Smooth bumper how-to
just_say_meth replied to just_say_meth's topic in [Archive] Wiki Submissions & Collaboration
Ok, since you twisted my arm :lol: I'll try and do it in the next few weeks and hopefully write it up by the end of the month :D Need to finish the TT bumper first though :lol: -
Smooth bumper how-to
just_say_meth replied to just_say_meth's topic in [Archive] Wiki Submissions & Collaboration
Anyone given this a go yet? Once you get started with this, you can turn your hand to most things. Doing a TT bumper for a mate at the moment, soon to be followed by an S4 bumper for myself :D Sneeky pic of TT bumper (Sorry it's a schitty phone pic) If anyone wants me to I could follow this up with a guide to smoothing and removing the rear towing eye hole? I've done a few of those now and I've also got a couple of scrap rear bumpers, but could just use one for the write up?? :norty: Andy -
Smooth bumper how-to
just_say_meth replied to just_say_meth's topic in [Archive] Wiki Submissions & Collaboration
Oh yeah, forgot Part 4 PART 4 Take to local bodyshop for prep and paint :lol: :lol: :lol: :wink: Sorry I'm just terrible at prep and paint :nuts: -
Smooth bumper how-to
just_say_meth replied to just_say_meth's topic in [Archive] Wiki Submissions & Collaboration
PART 3 Ok, so now you want to work with a flat bladed iron if you have one. I work in 1-2" sections. Firstly I heat the section up by moving the iron in and dragging the plastic to build up a small barrier, then with your strips of plastic start to melt small pieces of the plastic in and drag them up against the barrier. Sort of like building a dam and then pressing the next melted sections of plastic against the dam. What you have to remember at all times is you are tryong to bond these plastics together (bumper, panel and strips) so ensure as you are doing this that they are all melting and becoming one piece. You will soon start to tell if this isn't happening, when it cools a weak section will pull out pretty easily. So working in the sections, using any method which combines the plastics, stabbing, dragging, smoothing. Pressing the melted plastic against the dam, slowly work your way across the section until it's filled to or just over the level of your bumper/panel. Then heat the next section up and work along. The reason I do it this way is because if I work in small sections and heat the plastic first, the plastic rods I then melt in combine nicely with the plastics from the panel and bumper. You will notice though, working with the iron in the channel too much will heat up the plastic a lot andit will stay fluid and may move when you are working with the iron tip, so to combat either go get a cuppa or work on another section and come back whenit's cooled off. I know this is a lot to try and read and understand but it does become occurant when you are doing it :lol: Right, so a pic of the first section I worked on is in order And not a great close up shot but this is me working the plastics with the iron. What I'm doing is working the plastic toward the dam with the rear of the iron tip and with my other hand I'm holding my plastic rod which I insert into the channel and melt, then push backwards against the dam, and so on and so forth. In this pic the corner section has been done and flatten with the iron tip but the lower section to the left is still to be done Right, it'd be pointless showing pics of every section once done, but by now I'd have hoped you would have the hang of it so, in the immortal words of blue peter, heres one I prepared earlier :lol: Nah only kidding, heres what it should look like all the way round after your done welding. Now the plastic is probably all cooled off but give it 10-20mins to go totally solid before the next step. Alright then, now you should have something which resembles a smooth bumper, all thats needed now is to sand back the rough plastic and leave you with a surface that can be prepared for paint. So grab the orbital or sanding block or just some good old sand paper and get cracking. Remember if your keeping the swage line at the top don't go too crazy when sanding and remove it by mistake :nono: So after all that it should now look like this If you pull away any bits of plastic or there are any sections that you think sit too low then repeat the welding and then sand back again. Just repeat that till your happy, my aim when I did my first one was to have a bumper as strong as a factory one and to have only the lightest of light skims of filler over the top of it. When your happy, give yourself a pat on the back and stand back and admire 8) A wee test the guy at the bodyshop did to check my work was to push down on the panel and the welds and twist the bumper, he was trying to pull up any weak areas before he prepped it. I'd advise you to try this yourself, it will show you any areas that aren't 100% so you can go and re-work them or it will give you piece of mind that you did a good job. Hope this helps some folks, sorry if this last step is waffle but the only way I can describe my technique/process is in type, the pics can do a lot of talking but you would have to have loads and loads. As always, feedback is welcomed, if anyone wants to add or edit or submit then feel free :salute: If MODS or anyone who works on the wiki reqiures copies of all the photos I've used in the article then please get in touch. Heaven forbid I fall out of love with my corrado but should that day come or the forum outlive me or photobucket messes up then at least the photos could be restored :D Andy -
Hmmmmm :scratch: Meth - which pin went on top/bottom? I didnt notice the pins different when i took my brakes apart, so theres a chance i put the pins back the wrong way round.[/quote:b1371lf6] I don't know, I've done exactly the same thing :lol: I can't find anything to say which pin goes where, I've looked on Vagcat, here and the book of lies (Haynes manual) and drawing blanks all round :shrug:
-
Just checked my guide pins and they are indeed different, one is the same thickness all the way along but has a flat section along the shaft, the other is stepped with a taper. Both seemed to slide easily in top and bottom holes of the carrier. Although the tapered one had play in both holes. I'm totally confused now :lol: and the search isn't bringing back anything new.
-
Cheers, wasn't shedding any light when I tried though :( So the carriers are identical but the slider pins are different? one goes top ones goes bottom? I'll give the search a bash now :salute:
-
Hey Steve, Yeah I thought that they looked exactly the same too :lol: Certainly can't see any distiguishing features!! Would be good to know before I bolt the whole lot on though. Cheers mate, would be good if you could check :notworthy:
-
Hi Folks, just a quick question. I'm finishing off my rebuilt rear axle and when I was in VW today I asked the guy if the caliper carriers were sided, to which he replied yes! So my question is how can I tell which side is which cause the part No.s are no longer readable?? :lol: TIA Andy
-
Good Salesman & Good Buyer Thread
just_say_meth replied to VR6's topic in Site Comments and Questions
Thanks Jon, good doing business with you 8) fast payment and good communication, what more can you ask for in a buyer?! :thumbleft: -
Smooth bumper how-to
just_say_meth replied to just_say_meth's topic in [Archive] Wiki Submissions & Collaboration
:scratch: Seems to be cutting the right hand side of my images off, ho hum, nothing important has been cut off 8) -
Smooth bumper how-to
just_say_meth replied to just_say_meth's topic in [Archive] Wiki Submissions & Collaboration
Part 2 So if you feel that the recess has had plenty of time to bond and that it is stuck down securely you can remove the clamps and you should be left with something looking similar to this It should sit comfortably around all edges and sit flush (not proud cause you will need to get a skim of filler over when prepping for paint) to the height of the rest of the bumper. We can now move on to the fun part, so put those soldering irons on and grab a cuppa :) I used two irons for this job, a small cone shaped iron (ebay for about £3 and it has adjustable wattage) and a larger headed one with a flat tip for smoothing out the plastic. For this first job I used the smaller of the two So running the tip between the two edges the plastic will start to melt, I work in sections 2-3" long and move the iron slowly backwards, then let it stab forward and work along the section with this stabbing technique, ensuring that I am melting the plastic from both edges to weld them together. For larger gaps, insert the tip further but make sure the technique is doing the same job, melting both sides of the plastic and welding them together. So work round the whole recess, stabbing/melting/welding as you go till your happy and the gap now looks similar to this Now when that has all hardened, which takes 2-3mins, so by the time you have finished one section the previous section is usually hardened etc. (Now if you have a second flatter iron use this for the next steps) You can start to fold any excess plastic from the stabbing action into the gap and flattening it down with the iron tip forming more of a groove around the recess Continue around the recess until you have a channel that runs the majority of the way round. In some areas you may have been able to completely fill the channel. Next cut yourself some strips off your donor bumper and remove any paint That'll do for tonight :lol: I need to figure out in my head how to articulate myself into text :lol: It's not that the next part is hard but it's the type of thing that easier to show someone than to put into text! Bear with me, I'll get it finished soon :wink: -
Right Guys, I was smoothing the front plate recess on a bumper the other day and it popped into my head to write a how-to guide. This is the first time I've done this (writing a how-to) so please bear with me :lol: by all means this isn't the only way to do this but it's the technique I have adopted so feel free to adapt it to your own style. I missed a couple of photos out at the start but shouldn't affect the process and maybe someone else could submit these if they give it a bash. This is my second smoothed bumper using this method and both have turned out well and strong/flexible so the bumper maintains it natural strength. So the aim: To fit a plastic panel into the front plate recess and to plastic weld it into place. The finished result will be ready to be prepped for paint and will give that US-Spec stylee bumper. This process when done properly leaves you with a very strong finished item but will flex just like bumper would as normal. Unlike using filler etc to fill this recess it will not crack or split. Time: This can be done over the course of a weekend, leaving the bumper and panel to bond overnight. You will need: 1xBumper you want to smooth 1xDonor bumper (early or late, doesn't matter) Stanley knife, with a few blades Dremel or other type grinding tool with sanding tube attatchment Soldering iron(s) 1xtube of Tiger seal and squeeze gun Sand paper or even better an orbital sander and discs Some clamps to hold the panel in place while bonding it. Cost: I had most of this stuff already from previous plastic welding jobs but I think it could be done for around £60. My bumper cost £30, the donor bumper was £10 (Thanks stevej) and then tiger seal, sand paper, soldering iron, clamps etc can be bought reasonably cheap if you shop around. PART 1 So to start, get your donor bumper and cut out the front plate recess, giving plenty of room around it so you can trim it into the perfect panel to flush mount into your bumper. You should end up with something like this: [iNSERT PHOTO OF ROUGH CUT PLATE RECESS] Next using your grinding tool trim down the plate recess to look like this one: Now you want to take the paint from all the edges you are going to be welding, on your bumper. So use your sand paper or orbital sander or grinding tool. so all around the plate recess and then you want to do the inside edges of the recess too. For this I used the grinding tool and from now on it will feel like your best friend :lol: Being careful to sand lightly to only remove the paint/primer and leave a roughed plastic surface Now we have all the edges free from paint and a rough plastic surface to work with, we need to trim the plastic panel from early to perfectly match the plate recess. It will be mounted flipped over and into the recess, so a quick line up and you can see how much will need to be taken off to fit So taking the edges down like so and checking often to see how much more material needs to be removed. Remember don't take away too much, it's harder to replace it later Now I didn't take a photo of every edge as I removed material, so a bit of common sense as to how much to remove to make the panel fit well. Best practice is to fit the deeper edge (Top edge that sits against the swage line) and the side edges then to trim the lower edge to match the depth of the recess Trimming lower edge Now after much trimming and many test fits you should have something which sits comfortably against all edges of the recess. I removed a little too much from the lower edge early on, which resulted in a slightly bigger gap at the top edge, but don't worry if this happens, it can be filled with plastic later. Top edge should sit closer than this: Now we have the bumper and panel ready it all has to be glued into place so you can concentrate on welding the panel into place. For this I used Tiger Seal, it is a very strong adhesive, so you don't want to get this anywhere but the inside of the recess :nono: So lay a bit down in the recess and then get ready to place on the panel and clamp it down. I left this overnight to bond properly before starting to weld :sleeping: Now go get some sleep cause the next bit takes a wee bit of time and a good bit of patience. Next part to come, I've got all the photos, just need the time to write it up. Any feedback is welcome :thumbleft: Andy
-
Evening guys and gals, this is a long shot but does anyone happen to have the engine out of thier G60 and could take some pics of the wiring for me? Just building my G60 back up after paint and would like to see pics of the factory routed wires, see if I can tidy the install up a bit in the process. Should have taken pics myself but I forgot :( Pics I would like would be a shot of each chassis leg, fire wall and rain tray, if it's an ABS model that would be even more helpful :D Many thanks Andy
-
Alright andy, didn't know you'd done the wheels already!! First time i've been on the forum in ages and noticed your thread. No doubt mike has told you my cars in for paint, can't wait to get it back :D Just trying to gather some stuff for a second trip to the powdercoaters :lol: got some pics when I was up seeing the car today, i'll pm you a link. Howd you get on with the appendix op?
-
I've added Awigman and critical_mass My number is 0216-1043-1321 Feel free to add me if you wish :D The Hub- I'll add you next chance i get mate 8) P.s I should come up as andyG60 :wave:
-
Must have missed this post :brickwall: Bought it last week, great fun, been trying to split my time between it and the corrado :lol: Misses loves it too, she should be studying but seems to have won quite a few cups :lol: :? I'll post up my code when i get home :D
-
There is an early (12 gallon) and a late (15 gallon) tank, your G probably would have had an early tank but i think either should fit :D *EDIT* My bad, guess either won't fit judging by Yandards post below :(
-
If there ali dishes then be reasonably careful, don't think there is any rhyme or reason to getting these off but i just kept running the stanley blade around then tapping with the mallet and vise versa :)
-
I'd check this first off, also check the knock sensor is connected properly, guy i know had major running problems, stuttering/holding back, turned out he hadn't connected his knock sensor after doing something else in that region of the engine :eek:
-
Got that problem too :lol:
-
It's really coming along mate :salute: Those fans sure do give you a lot of clearance, I'm using the rallye rad & fan and it's going to be reasonably tight :lol: Will it be ready for the VAG show? can't wait to get a look at this car in the metal. Andy