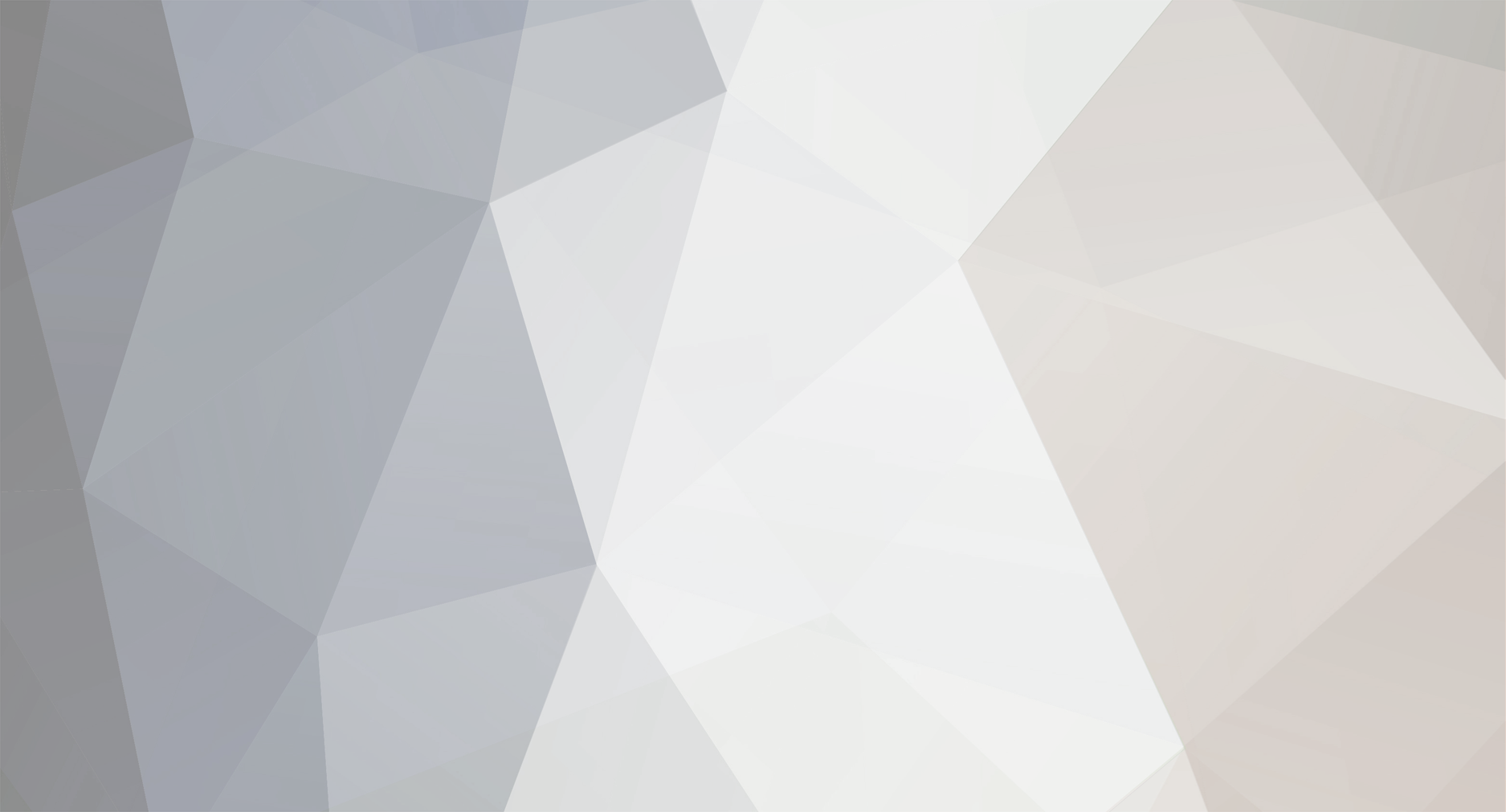
oneohtwo
Subscriber-
Content Count
623 -
Joined
-
Last visited
-
Days Won
7
Everything posted by oneohtwo
-
I've done this a lot recently, but mine doesn't have the rubber grommet, just the metal washer and the plastic spacer. Might have to look into that, but otherwise yes the order is correct. I've always felt it seems an odd design, because there's not a lot actually clamping it to the bulkhead - perhaps the rubber grommet is key. I don't think there should be much slop in the wipers at all - your 2 cm of slop is likely due to the worn nylon bushes on the flat link arm that goes between the wiper motor and the wiper mechanism. I have been experimenting with potential replacements, and the prototypes on mine have removed the slop completely. The wipers can be positioned correctly, and will no longer hit the scuttle trim, or the side of the windscreen. I have just received a latest batch of bushes so will see how these go. There is another thread in here where I have documented my attempts.
-
I've got a vague feeling that you need to adjust the com port speeds on you Laptop to get it to communicate with some modules, ABS might be one of them. I remember doing this to mine, although I can't find the guides now which isn't too helpful I know! But hopefully that might be a starting point.
-
Yep. It's a pretty nice area all in all (I accidently left the passenger's door on the latch for a couple of weeks once and nothing happened to it) so I think it's just careless more than thuggery. Plus delivery drivers who couldn't give a shit either way. Exactly this. It's disheartening looking at it with dings and scrapes all over. I think a mobile dent repairer and having a go myself with rattle cans might be the cheaper compromise. I did do a bit myself years ago on the A-pillar and it looked fine for a while. Although now looks like crazy paving on the clear coat - not really sure what causes this. And yeah, I can only assume people just think it's an older car so isn't worth anything. Like I say, there are plenty of pretty nice cars down the road with not a mark on them. The only others in a bad way are an old Volvo XC90 which clearly is just being used and abused and a 90s Polo and 406, both of which haven't been cleaned for decades and are losing all their clearcoat. And then mine.
-
ABS pump looks nice. Who did you get to refurbish it, or did you do it yourself? I had mine refurbished, but was a bit disappointed they didn't tidy up the outside!
-
Not a great weekend for the Corrado. Went out to clean it yesterday and as I got to the front found some lovely person had done this: Amazing really. Whatever it was was at the perfect height to just scrape over the bumper, but also low enough not to damage the bonnet. Not fully sure what to do about it yet. What I don't understand is, I've checked all the cars along the road almost all of them are in near perfect condition. Just one or two slightly older cars with some cosmetic scrapes. Then you get to my car and near enough all 4 corners are scraped and dented, plus the rear bumper and now this. Is it because it's an older car people just think it doesn't matter so are less careful? Or it's just smaller than most modern cars so they don't see it? Apart from the scrapes and dents the paint is looking in a bad way. Clear coat peeling here and there, crazed areas and tiny rust spots. No way am I going for a full respray whilst it's parked on the road - but it would be nice to get it looking somewhat smarter.
-
I was also going to add, if anyone does want a pair of the workable push in types in the interim (without the circlip) then please let me know and I can see about getting a batch of those done.
-
I had another batch of these made up to suit the circlip option, and have given them ago. They're not entirely satisfactory though: 1: I miscalculated the measurement and the circlip slightly deforms the bush. This isn't a major issue, but not ideal. 2) I didn't allow enough tolerance on the circlip slot, so that the circlip pushes the flanges up when inserted. I'd be a bit concerned after a while it might shear off the flange: 3) And as it just slots in, it's not really tight enough in the whole, so the whole bush rotates in the link arm - including the circlip. We don't really want metal rubbing on metal. So, I put my original push in versions back on the car. These still seem to work well, and took a good deal of effort to remove so they are pretty secure. One end had very slightly pulled out the hole, which I think is due to the angle of the wiper linkage at full extension, but didn't look like it was going to move any more. And at any rate it is in the direction that means the link arm wouldn't actually come off. So, I might revisit the circlip version. Correct the mis measurement, and increase the size of flange on top. I also might give the middle section a bit of a flange so it compresses into the link arm hole and will hold fast.
-
Looks like you've lucked out there, the Recaros are rare and highly sought after! Back is definite Corrado, but the first aid kit doesn't look OEM. OEM would have VAG branding on it somewhere I think. From memory VW used various different kits so hard to say what an original is (Although I might be thinking of the warning triangles), so I don't think it's something to be particularly concerned with.
-
Just to keep this updated, I have modelled an alternative to use with these circlips: 12mm x 10.45mm E Clips (DIN 6799) - Marine Stainless Steel (A4) (accu.co.uk) So I will get a test run done to try them out. Probably next month now, as I have been away and it's been an expensive month already. If they work OK, I will offer those for general sale. On the plus side the set I fitted to mine seem to be holding up well. Been on a couple of longer runs where they were needed in some heavy rain and don't seem to have any issues. All seem to still be nicely in place and keeping the linkage tight, with neither wiper fouling the windscreen trim. Very nice not to have the thuk, thuk, thuk accompaniment on a particularly rainy journey now!
-
1996 Corrado VR6 Flash Red Chelmsford to Cheshire 228 Mile Roadtrip!
oneohtwo replied to G60MAT's topic in Members Gallery
Nice! I quite like those alloys, and if they were a dealer fit item then you could keep them and maintain both an OE and individual look! Certainly look better than the 15" Speedlines otherwise. On the other hand I quite understand moving up to 16" wheels. The BBS 15s on the earlier models seem to look fine, but the 15s on the later models just look undersized. -
10 Points to this man! One of the passenger side engine mount bolt had worked loose, that's another one sorted.
-
Think I may be in a similar position to you, seem to have plenty of moisture in the car at the moment. No big puddles fortunately, but there's always a lot of condensation on the interior of the windscreen and rear window. So much so it had frozen in drips the other day. My hunch is that it is the sunroof as it can't be vast quantities of moisture getting in because the carpets aren't soaked (although they do feel a bit damp), but I suppose I will have to start getting trim off. Have you fixed the issue on yours?
-
Thanks all! I am just debating whether to try a third type with a circlip. Easy enough to do, but there's aways a minimum order with the 3D printing each time unfortunately. It is potentially a neater option though, the one as is seems to work OK, but obviously it's a bit odd to have it part of it shear off in the process. Especially if distributing these to others. Good to know that there's 4 people on board for any more though. Here's the missing picture of it on the link, still haven't got the videos uploaded though: https://am3pap007files.storage.live.com/y4msAR0Ri7-xk-2My6j8QVhRdhK3wC1B4dgBDlCdedH70Irrwga2D1R-oPHjvUsAHb3KmDSW9uZWaKGEERZsft6th7v98GLOX_Um-4JXXR3L7iPRGdilu8sVAJ9L6dG94nRRmgw4JxyaSMUa5SxF1R0Ce5yMJBAAwsx1nH_FkLrrbPh-AKoo1XeKOoCkR_XKlHQ?width=1024&height=576&cropmode=none (I don't know why they aren't showing in the post, they always have done when I paste the link in)
-
Ah nice work, thanks. How did you get them to show? I linked the wrong last image, but they're still not loading for me.
-
Update on this: Success! I redesigned the insert with a tab on one side instead of the big flange in the hope it would push through and spring back out, to clip in. That didn't entirely happen, as the tab just compacted in the hole, and then sheared off. However, it did mean the insert is extremely tightly wedged in, so that it is actually secure. I certainly couldn't shift by pushing down on it on a bench, so I went ahead and installed it, and it worked! Ran perfectly and there's absolutely no play in the system. No more wipers hitting anything! This is what it looks like: https://am3pap007files.storage.live.com/y4myI3eneG6JOEv2jfdAiWnmOC0PFmg8jqVFVwHat7GSdjQEaHTKdMKUTZZLOD4zD6hIhx0sQ9dv3dlj_SqDsqQ2DyiW0E8SlDEeHlIStp6lOinzafdWwBIXChX6yRjWBZQBaiz1_F61okD7oSaC0-UpLYRtDPo6zFmLZj_NaEUH-qJOuGfZO5zVzKy4FoMf7Ld?width=1024&height=576&cropmode=none https://am3pap007files.storage.live.com/y4mfMSETEjD3LF139vV6VP_LANSE3KgMeyO-cQE_6lnVQRfEmSAVkm3dUJfNb4fhc4vR8GPfFS165A4JP2UXMyaRAG_fJCuX7EfRlokNpGxFFHBfx1KEn0UtXHHgFneNBBU_oPErdX-dYj3cTik_WtU8a3qF4J4q8a2P-01o5iz9XF1RaAlp8A0KZgt0P28pzCS?width=1024&height=576&cropmode=none And installed: https://am3pap007files.storage.live.com/y4maM1NwFspZgBSkK-6_FPd9biHzz8QbXKCNUSCJFjMEhDcuEkN5ChnPkhXn1QsAQCxpkFyrbwH9ikAmKK1nlDY_hC9iqu0JiT80K8DE--MrcUNxNgH5XG32d9uaL4Od_sQtoHPS5rwt2V6tQT71Vi9MmG9yW6wTkjmcVvdbHkzYitvYtisdvLzpJsfjnSY1N9X?width=1024&height=576&cropmode=none You can see the tab has compressed, so it is held in by friction. And this is it installed in the linkage: https://am3pap007files.storage.live.com/y4mfMSETEjD3LF139vV6VP_LANSE3KgMeyO-cQE_6lnVQRfEmSAVkm3dUJfNb4fhc4vR8GPfFS165A4JP2UXMyaRAG_fJCuX7EfRlokNpGxFFHBfx1KEn0UtXHHgFneNBBU_oPErdX-dYj3cTik_WtU8a3qF4J4q8a2P-01o5iz9XF1RaAlp8A0KZgt0P28pzCS?width=1024&height=576&cropmode=none You can see that even just being held in by friction the insert isn't going to pull out of the link arm as it's acting in the opposite direction. And the ball joint is nicely held by the shape of the insert so that isn't going to pop off either. It's very snug and tight, but does allow rotation and swivel around the ball joint. I do have some videos of it in action, but unfortunately they haven't uploaded properly. I will post if I can get those uploaded. So, I think we have a solution! I have, however, only just twigged about JJBRADO's suggestion of a circlip for some reason, so that might offer a bit more security especially if other people wanted some and were nervous about it just being pushed in. The 3D printed versions also seem up to the job, so I am not sure whether to continue exploring CNC machining options. The finish isn't amazing, but seems good enough. I am happy to run with these for a while in day to day use just to see how they hold up, in case other people wanted to get a better idea of durability first. They may not be as durable as the originals but I think we just have to consider them a disposable item that we can swap out when they get worn. Either way I am happy to take views on this. Let me know! EDIT: I can't get the pictures to load for some reason. Normally they just embed straight away. Will try again later.
-
😂 They certainly got the stopping bit sorted... Thanks on the MAF tip, that backs up my initial question so I will get some cleaner on it first. Clunk is still a bit of a mystery. Checked the bumper bolts and all seem tight. Haven't looked at the drop links yet, but I'd have hoped the mechanic who did the tracked would have noticed these when I asked him to look for anything. But you never know, so will go there next. Think I may have to take it to a garage to get to the bottom of it.
-
Oh yes, I remember your travails. Glad you got it sorted. I'll have a look at the bolts, good thinking.
-
Hello Folks, Got two odd issues I thought I'd combine into one thread for ease. First an odd rattle/clunking coming from (I think) the engine bay. This has been going on for months and I keep finding loose things, tightening them up thinking it'll fix the issue but it doesn't. I got the tracking checked and corrected and asked the mechanic to look for anything loose under the car, but no dice so I think the drivetrain is fine. But now I think I have traced it to the gear shift tower as it appears to be the only thing loose left in the engine bay and when I waggle it (the mechanism with the counter weight) it seems to make a similar sort of sound. The rattle/clunking happens when going over bumps and rough road (unsurprisingly) but also at slow speeds when lifting off (although may happen at speed as well and I just can't hear it). Sometimes there's not much rattle, but others a lot. Sometimes there's a bit of a clunk. Sometimes it's more a shaking rattling type noise. Could this be the gear shift tower? Obviously it needs to be able to move freely, but I've never noticed it rattle like that before. All the nuts and bolts appeared to be tight on it, and there's no issue changing gear. I'll try and get a helping hand for someone to rattle it whilst I sit in the car to see if it sounds the same from inside, but in the meantime does this sound plausible and anyone got any reason why it would be? Second issue is the engine stalled whilst I was slowing down from 70 to 40 on the motorway for some road works. It was what I'd describe as a leisurely gear change down, so when I put the clutch in and before I had selected a gear I noticed all the red lights flash up on the dash. No real dramas as I popped it back in gear, gave it a bit of throttle and bump started again, but it's not something you want occurring. This used to occasionally happen, particularly when hot, when pulling up to junctions etc. where the idle would drop too far and stall. However, I have refreshed a lot of the throttle body area: new ISV, new dashpot, new PCV, clean throttle, and removed the slack in the throttle cable, so it is generally running pretty smoothly. The throttle shouldn't be snapping shut too quickly for the ISV to respond due to the dashpot and the ISV shouldn't be sticking. I am therefore wondering if possibly it's the MAF and that could do with a bit of a clean? The other things I haven't renewed are the fuel pressure regulator, and Cam position sensor.
-
I typed a reply to this, but apparently it didn't submit! Anyway, I think I slightly misunderstood, as per fendervg, you do need to get the heater box out. I got mine out without taking the dash out, just the centre console and under dash trims. I don't recall it being too much of an issue after that. Think the bolts through the bulkhead were the hardest part. I used felt from a hobby shop, and if you can get sticky backed then that's probably better. If not chose your glue carefully. I used a household general purpose glu (gorilla glue from memory) but it smelled quite bad for a long time after. Still smells a bit odd on heater setting, but don't know if that's the glue or something else. Also take care that the felt doesn't foul the hinges. I made a piece slightly too big so it slightly obstructs the hinge, and I can't "click" the temperature dial at the end of turning it all the way to cold.
-
I'll just put my name down in this thread as well, in case numbers build enough for a re-run. Driving in France recently wasn't super fun with the Corrado headlights!
-
I may have misunderstood, but yes as per fendervg you need to get the heater box out. I took it out without removing the whole dash. Think I gave myself a bit of time and did it over a weekend, but it's not a massively time consuming job. Be careful what glue you use to stick the felt on though. I used a fairly normal household glue (gorilla glue I think, just the general purpose stuff) but it smelt quite bad for a while when I had the blower on. Still smells a bit odd if I have the flaps open to the heater, not sure if that is the glue or not these days, as it's been a good 10 years or so since I did it. Also be careful to ensure the felt doesn't obstruct the hinges. I cut mine a bit too large so when turned to fully cold the knob doesn't quite "click" into place at the end of the turn.
-
It is, I've done myself. Was a fair while ago though, but I don't recall it being a major hassle. I don't remember much specific though unfortunately. I think once the under dash trim and centre console is all out it's fairly straightforward. I think the screws through the bulkhead were the most difficult.
-
Update on this, the 3D printed parts arrived, and actually they're not bad. They look like this: I had them vibro polished which made the finish a bit smoother, not really sure if they would be appropriate for the final product, but I feel better about it as an option now. However, the main issue is getting them in the link arm. I had envisaged this being an issue, as above I am fairly sure the originals are moulded onto the link arm, but hoped that a solution may present itself once I had them. However, having given it ago it's a definite no, as there's no way I can see that the flange goes through the hole even with a bit of heat. So a bit of a redesign is needed. I think the solution is to reduce the size of one flange and turn it into a chamfer that will initially fit in the hole and then hopefully push through. Probably have to be after Christmas now. But this has given me hope that we could solve this!
-
Hmm, not sure. Maybe I didn't get a good enough mix of hardener. Seems an odd product though as there are plenty of reviews online that have had the same issues as me, and others which it's been fine for. On Amazon, it's got a rating of 2.7 stars. The reviews are either 1 or 5 star!
-
Ah interesting. Did you do it long ago, and has held up since?