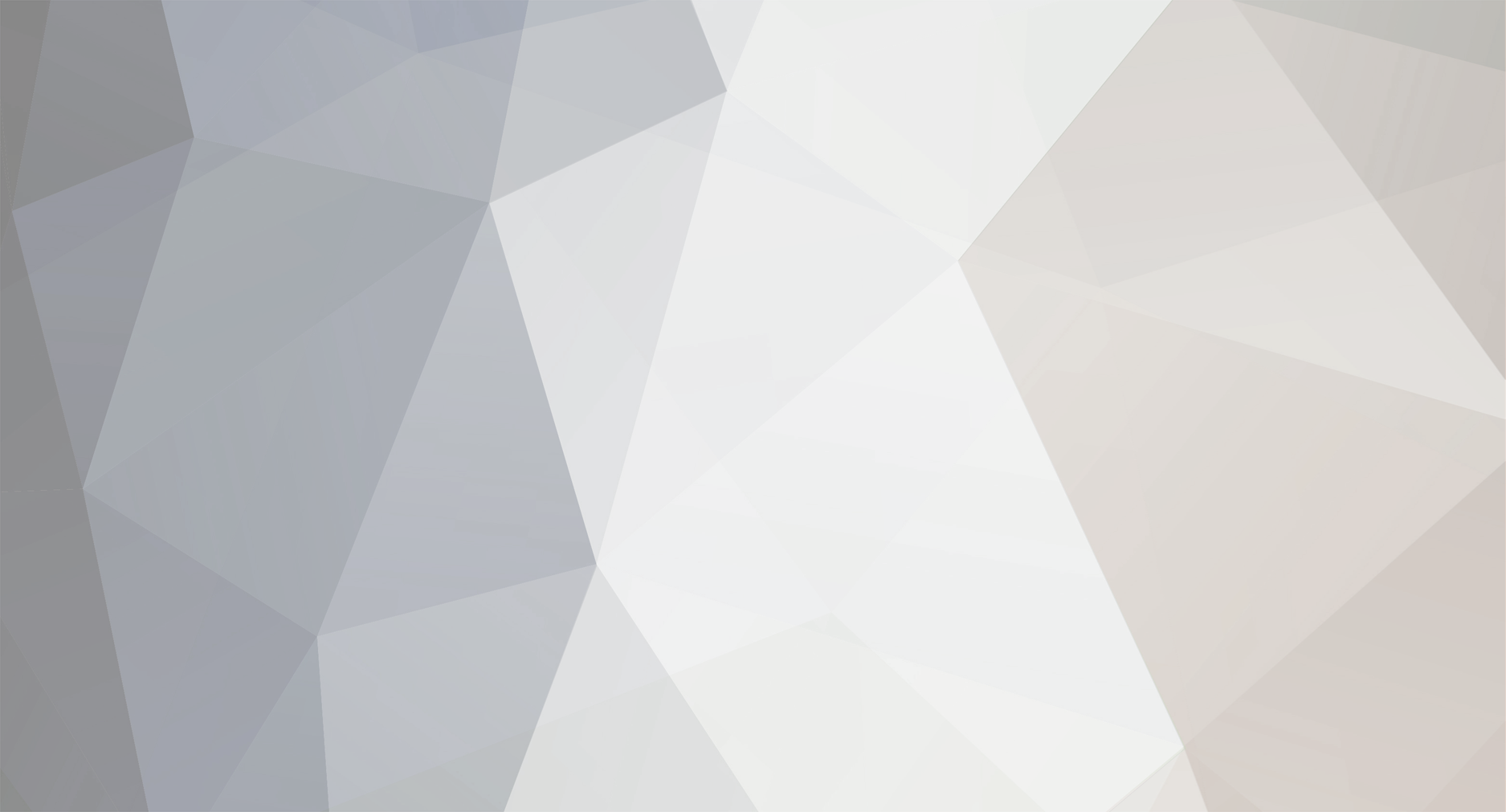
oneohtwo
Subscriber-
Content Count
605 -
Joined
-
Last visited
-
Days Won
7
Content Type
Profiles
Forums
Blogs
Calendar
Articles
Gallery
Downloads
Store
Everything posted by oneohtwo
-
Thanks, that all looks very clean and tidy at the back there! Trying to work out why mine looks a lot more cluttered...
-
Thanks, that's a great help. Not seen 7zap before but will keep that in mind for future reference. Yes, it is carbon moulded. Basically my old one was rotten on the inside and I ran out of ideas for a replacement! Best option I could think of was to mould one in carbon. There's more details in my build thread if you're interested.
-
Hi all, does anyone know if there should be a bit of heatshield against the bulkhead here: There's an extra pin here that looks like it should have one attached, and it kinda looks like there is from otherpeople's engine bay pictures but I've not been able to confirm. If so, does anyone have a part number? My searching has only turned up the lower one so far.
-
Ahhh, shame! Still at least you know now. I rather suspected after you said there was an issue and was now showing out of stock that there was an error on the listing and they never had any. Probably such a rare purchase that the listing was never updated. It did seem surprising at the time that Amazon would be the only place to have any!
-
Hmmm, that's not so good. I haven't ever had an issue with Amazon in terms of customer service, although I have never tried ringing them. A few times I have had items not delivered and there's options next to the order (not easy to find), and they've immediately just sent out a replacement. They are such a large company I don't think I would bother trying to ring though, can see why you've had issues! Odd that you can't cancel - usually that would mean it has been dispatched I'd have thought and in transit. Have you had any email notification it has been despatched? Might have gone in junk, but they always send a dispatch notification, worth a look. Also you can track the order from your orders page: They're not some two-bit organisation so you should be able to find out some info there. That should at least let you know if it has been dispatched or they are waiting for stock anyway. If it's been dispatched then hopefully all good and it's just a matter of waiting for the delivery company to sort themselves out.
-
Ah yeah, it does say 3-5 days dispatch, and the time of year and everything going on isn't going to help.
-
Has it arrived? I'm on tenter-hooks here!
-
Cool, thanks, mine did the same, so that's reassuring.
-
When you were doing your 288s I don't suppose you found the disc rubbed on the splashguard at all? The little tab that sticks out a bit and sits behind the ABS ring/sensor?
-
Fair play mate, at least you'll know either way. And it's a bit of a win-win. If its a knock off send it right back and you know you've got the best available in the Dasis, but if it is the genuine article you've got one of the few remaining Nissens/Hella rads.
-
Apologies! I know the feeling... Unfortunately the question and answer thing on Amazon is only answered by other customers (as far as I am aware) so we could post the question but I doubt we'd ever get an answer. It's not an independent seller either, so there isn't one to contact. The upshot of it being sold by Amazon themselves is they'd have a no quibble return policy if it isn't a genuine product. Having a look at their website Dasis specialise in cooling applications so should know what they're doing, and they manufacture in the EU, so I would have thought it's fine.
-
I saw the Hella sticker as well - the Hella ones were made by AKG so perhaps they were making identical ones for Nissens as well? It's sold by Amazon themselves so you'd hope they wouldn't be misrepresenting a listing. You're right the Dasis core is listed as 34mm on Autodoc - but then they also have the core dimensions as 630x310x24 which threw me. Don't suppose you have it to hand to do a quick measurement out of interest?
-
This thread peaked my interest from my rad search a couple of years back, and I thought I'd have a look around what with the Hellas now unavailable. Stumbled on these Nissens rads, on Amazon of all places! Nissens 65286 Radiator, engine cooling: Amazon.co.uk: Car & Motorbike Not sure how they are in stock on Amazon but not on Autodoc, etc... but it is the correct Nissens part number for the rado. Might be an option if the Dasis doesn't work out chap. I read on some other forum that Nissens may have made some OEM rads (Edit: Just noticed Bruno mentioned this on this thread as well), not sure about that but they seem similar to Hella in quality as far as I can tell. In fact the picture on the Amazon listing is actually a Hella/AKG. They both seem to have a thicker core than the other pattern rads - 35mm instead of 25. You can see on pg1 of my build thread the difference in thickness between the Hella and a cheapo GSF pattern part. The Dasis you have looks to have the thinner core, but the fin design and quality looks more like the Hella, so hopefully it's a good one. Bad luck about that ally one though...
-
Missed this one before, this is great stuff. Amazing how the time slips by. Redoing the underside looks like a horrendously unpleasant task! Great to know it is all in perfect condition. I like the idea of hiding the wiring so will be interested to see how that turns out - I've no idea how some people seem to be able to hide all the wiring, pipe work and ancillaries! How are you planning on getting the wiring out of the chassis legs out of interest? You're right about the custom exhausts droning. I have one, from Infinity, and whilst they have done a superb job with the look of it it does drone at, unfortunately, motorway cruising speed. Rest of the time it sounds quite good. Can you buy the Militek parts separately? Wondering whether I can just buy the back box and maybe keep the rest of the system as is. Also is that the plastic cam cover you have?
-
Thanks all! The gearbox was certainly many tedious hours spent on the floor with a variety of wire wheels... worth it in the end though. Block and head were largely Stealth's work. Had some help from the gf guiding it over the crossmember, but then she had to continue working so I was wrestling with it by myself to get it on the mounts. It seems you need a precise alignment of the crane, leveller, planets etc... to get it in. And then a bit of brute force. Few bits of paint scrapped off here and there which is annoying, but I think should be fixable in-situ. Shame to spoil the hard work! Knocked up a little stainless steel bracket to support the belt pulley splashguard as well: Wasn't going to bother as initially I thought it'd be too much hassle, but then seeing how close the guard is to the pulleys I thought best not to have it flapping around, and it was fairly straightforward in the end. Of course, had to make some adjustments after it was attached to get it around the crossmember. Turns out the cut out on the original is there for a reason! The rad support itself is noticeably a lot less stiff than the steel original once on the car. A little annoying in that I was following professional advice, but if I'd known a bit more I may have made it a thicker. Although having said that, it is only the front lip where it clips to the bumper that has a lot of flex and once it is all clipped in should be stiff enough. It definitely seems strong enough with the cross member bolted on. Took my weight OK on the engine mount in a not very scientific test, without any deflection though, and I am probably not too far off the load on that front mount. I think the engine all in weighs about 200 kg, hard to know the distribution but I suspect at least half is on the front mount, and I am 85kg or so. I think I will use one of the failed attempts as a test bed and do some load testing if I get a chance, just to see what ball park we are in.
-
Momentous day today... after a a year and a month on the stand the engine is back in the bay! My word, you realise it is a tight fit in the bay when you try and get it in. Was a job and a half, a good 2 hours or so of wrestling it in. Getting it over the cross member wasn't too bad, but for an absolute age I couldn't align it on the mounts. The exhaust downpipes hanging down get in the way nicely as well. Will have to assess the damage in the morning, but big relief to get that back in before the end of the year. Getting the gearbox on went fairly smoothly: Anyway, can sit back and enjoy Christmas now, the fun part of bolting things back on can begin in the new year!
-
Plinth looks good. Has it still got all the lugs on the back?! Was that a special plastic paint you used? Was thinking of doing the front grill.
-
Yup. if it's the one thing I have learnt more than any other throughout this build... Anyway, the thing won't undo now, oddly. I can't get it back out so there's not much to be done. Hopefully I'll never have to remove the engine mounts again so I can just forget about it.
-
There's always bloody something isn't there! One of bolts for the transmission mount where it attaches to the subframe has stripped it's thread. I can't get in there drill out the hole, so all I can think is to get a longer bolt and add another nut on the end...
-
Yeah, It's quite difficult with carbon fibre because strength and stiffness all depends on the thread direction. For instance the stiffness is similar to steel, but really that is just the carbon fibres themselves, when you add in the resin being 40% or so of it, it drops to about half, and then if half the fibres are running the other direction (with the twill weave) it may half again. From the checks I have done it should be fine, but I will keep the engine propped, which I would have done anyway with the original. Thanks! I didn't pull the alternator apart so I couldn't tell you I'm afraid! I sent it off to a company to do the refurb and they did all the internals. They sandblasted the cage back to clean metal - when I got it back I just masked off all the holes to paint it.
-
The were the Febi ones, rubber as a straight replacement for the originals. got them from Murray's Direct on ebay- Keyo has recommended him before, and does seem to get a fair bit of decent quality Corrado bits in.
-
Ta, problem was I didn't have a socket big enough to fit over the hole - otherwise that method looks a lot simpler! Managed to rig something up with some offcuts of wood lying around: Which is a bit Heath Robinson, but it did the job with a bit of wrestling.
-
If anyone has done this with the original rubber ones (or any!) how did you get them in?! All I read about it is that it's an absolute arse - been trying to compress them, or pull them with a bolt in but no luck. It either slips to one side and so won't go in, or, if it is lined up straight, because the tapered end is bigger than the hole it just sits around the outside getting bigger the more it compresses. Plenty silicon lubricant applied but still nothing.
-
Yes indeed! Hopefully can crack on with the rebuild now! Shame they got rid of the autoclave - that does sound the best way of doing it, with prepreg carbon . I did it with a vacuum infusion method as surprisingly I don't have an autoclave in my garage! Just making steering wheels seems very niche? What does the rest of the company produce? I made a mistake when I said the carbon has similar strength and stiffness to steel. Its a bit more complex than that as they behave differently. Ultimately tensile (and so bending) strength should be higher. Shear strength is less (as lot is the resin component of this), and stiffness is also less. I made the fixing areas at the sides thicker than the steel original so that should be fine, and most of the stiffness is derived from the shape of the section, apart from the lower lip.
-
Thanks everyone! I did make it yep! I found a company called Easy Composites who do some very good tutorial videos and supply everything, which made it all look quite straightforward (because they're experts! 🤔) so thought I could give it ago. Turns out it's extremely unforgiving and mistakes were made. When I initially budgeted things I thought it was reasonably affordable (not cheap by any means but not unattainable), but that didn't factor in the mistakes and having to buy extra materials, and a lot of consumables, so I don't think it's something to do on a budget. This one was my third attempt, and my second mould so it did rack up a bit. Fortunately I am lucky enough to have the resources so that I could carry on, but for a while I did wonder if I was just throwing good money after bad. Thanks! I don't think you need any particular skills or talent to do it, just a lot of patience and perseverance, plus a bit of technical knowledge. I started doing this last Feb... and as mentioned had to do two moulds, and three attempts at the final part so it was extremely trying at times. I do now have a mould and when I started I partly had in mind that I could make some for others if it went well. However, given how stressful the whole thing was I am less keen 😂. I'm also in the process of moving house as well as trying to finish my rebuild so certainly not for a while. It's not just making the part, but positioning all the holes that is difficult, I've already missed a few a bit and had to enlarge them, tweak them here and there to get to fit - properly you'd make a template/jig, but I don't really have the facilities to do this. So I don't know. I may revisit this in future. I did give this a lot of thought before setting out, and I came to the conclusion that it's not really part of the crash structure - as Sean says it's quite lightweight and only really supports the rad. The bumper member is I believe the main crash structure. It is a large rectangular section so will carry far more load than the rad support and spans between the chassis legs - that will be taking the majority of load in a crash and transferring it to the monocoque. The actual engine cross member supporting the engine is much beefier as well, so will do more, although I have a feeling that in a major accident the bolts securing onto the chassis legs may well shear so that it drops down. The bumper is locked into the chassis if this happens, so again seems to be doing most of the work - that said having looked at my bumper, it's pretty rotten, with some sizable holes in it... 😬 The carbon fibre piece should be about equivalent in strength and stiffness to the steel original, as they two materials have similar properties, give or take, and the recommendation is to make the carbon piece a similar thickness to the original part. It is actually possible to flex the steel piece by hand in places even though it feels weighty. Only area of concern is when the bumper bolts are removed and the crossmember is fixed to the rad support only via the single middle M8 bolt - I have done a rough calc based on the weight of the engine and some known properties of carbon fibre at the more conservative end of the scale (structural engineer by trade), and I see no reason why it shouldn't do the job like the steel one. However, that doesn't account for the vagaries of the production process, and I can't really test it to destruction to make sure - so just to be on the safe side I have had a couple of steel brackets fabricated to sit under the carbon fibre which should provide some additional support. Will always prop the engine anyway so should be fine.