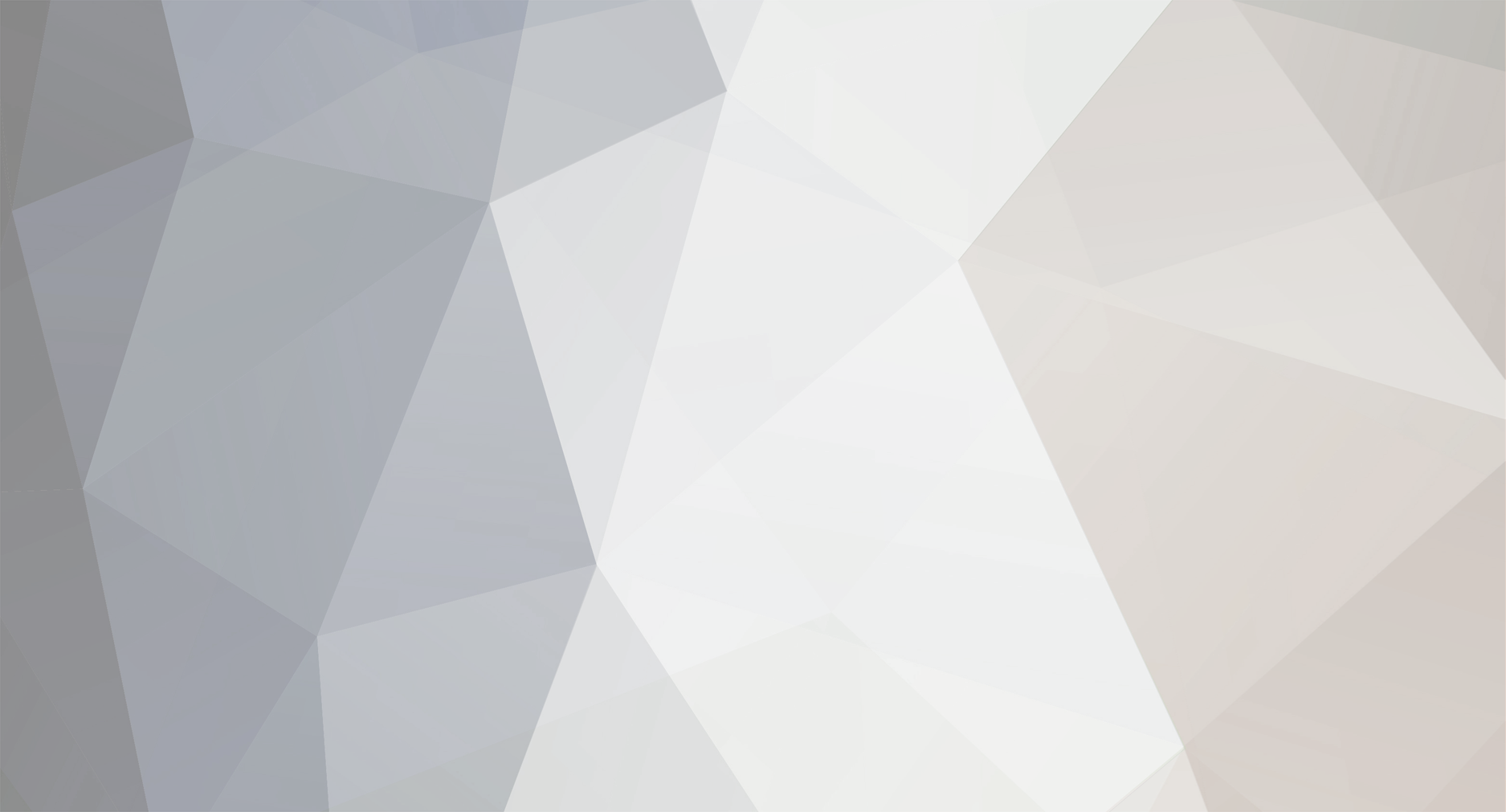
RW1
Members-
Content Count
2,091 -
Joined
Content Type
Profiles
Forums
Blogs
Calendar
Articles
Gallery
Downloads
Store
Everything posted by RW1
-
OT, but just make sure when the Scirocco windscreen rubber seal is seated that the whole outer perimeter of the rubber seal to body is then sealed with black mastik sealant, not silcone. Even the factory ended up doing this method after the early ones leaked badly. Bottom line, the windscreen rubber seal is a bad fit on it's own all round the edge not just the bottom corners. At "Scircco Comes Home - Onsabruck" in 1999 (big Scirocco/Corrado german gathering) they were fitting / demonstrating a Corrado screen fit (top tint banded screen replacement). All care was taken, body frame made ultra clean, everything going good... until the windscreen smudged/slid 3 inches towards the top left as they pressed it home on the adhesive. I think from then on I understood the german language very well thanks to the two german windscreen fitters! Dam ruined my photo sequence of doing a windscreen, never put the camera away so fast. Good luck in getting it sorted. No pride in craftsmanship these days. .
-
Cheers, but switch is shot for two reasons, the higher bulb plastic surround was brittle its fallen off since the photos so light "spillage" will occur and the clear plastic ring has melted and deformed. Different suppliers for one possibly - but more an improvement to stop the failures, also, the switches work differently such as daylight runing lights, non-dim-dip, dim-dip (UK market). Some perhaps the simpler switch version didn't put as much load on the levers as much as the dim-dip ones. The dim-dip version introduces a more complex sliding switch with more contacts.
-
Excellent, glad you got sorted. :) .
-
There is pressure to release in the fuel feed pipe but given it's leaking, that may be lost gradually given sometime. Expect upto 3.5 bar. Release it at the forward fuel filter coupling (not reverse flowing the filter then) and that can drop on the road into a pan. Fuel return pipe should not have pressure but just in case, undo the fuel filler cap to release any residual. It's the access that makes it hard, not the parts. Getting tools onto this area can be difficult as the coupling is almost into the channel in the bodywork. May be better on a LHD as the UK servo set-up isn't there.
-
Check the union joint in the engine bay. It's located almost in the body work. Follow the fuel pipes off the engine on the belt end on the rocker cover. They go off down behind the engine. At this point there is coupling where there the floor pan fuel pipes meet the engine's fuel pipes. The most likely culprit is the tank fuel pump to engine pipe coupling joint. Not too common but naff to sort due to location/access to get sealed properly.
-
Change the headlight switch tonite, just as well, it was on it's last legs with brittle and busted internals and working on one lever only. Good job I've got a box full in the loft. Photographed the switch but it doesn't show up the little lamp wiring as they twist around in parts of the switch where the camera angle is bad. Anyway, checked where the wires end up. As above in my original post, you will need to examine the external connections and where they run to. Each internal connection point for the lamp wire points will have a blob of solder and these are not directly on the other side of the plastic bottom plate where the loom connection pins are. So trace carefully as some connections travel half the length of the base plate. .
-
You may have an injector weeping. Suggest before starting when you expect it to do it, to take out the spark plugs and look into the cylinders with a torch and examine the piston crown for slight pooling on petrol plus if one stinks of petrol, this cylinder's injector is the one.
-
There isn't a VR6 back box separately. The replacement is a 16v or G60 box but gas flow rate will differ slightly and I'm not sure the pipe connection matches. So some gigerypokery will be necessary. It's on a curve and in the end I think you will need to drop the axle anyway. Axle brakes on rubber hoses and just mark/scribe everything before pulling apart to aid realignment on refitting. Surprised you bent the pipe. VR6 pipes are built like ships plumbing! Wished the muffler boxes particularly the middle one was the same. Price up the difference between the VR6 and the G60/16v alternative. It may just not be worth it as the forward connecting pipe on the new back box may be short and not allow you to take out the damaged part of the pipe. Certainly connecting the pipes on a curve will be trying. .
-
Agree Coolrado, back to metal as best you can and then treat. Have used it this way and 12 years on the rust hasn't returned on some of my repairs.
-
Not necessarily, could be two problems not related. Depends how rich and how rough, plus whether the ECU is set up correctly but no point in setting up ECU if the lambda is not working. Your man needs to do the check above on the probe.
-
VR6 Storm [238,500 miles and counting 13/02/07]
RW1 replied to CorradoWannabe's topic in Members Gallery
Yeah in the wrong place but that's dealers for you not reading the instructions. . -
H., The ignition illumination lamp is supplied via pin X, 12 volts, the earth is on pin 31 of the switch. The sidelight & head light illumination is on pin 30, +12 volts and when the switch is moved to sidelights/headlights and it exits via pin 56. Note this lamp has a diode allowing flow from pin 30 to pin 56 only. LED shorter lead is usually the -ve but check orientation using a 1.5 volt battery. I may be replacing my switch later this week. So will open up the old one later this week hopefully and photograph the plate connections. C. .
-
Its quite a small plate, unlike the patch plate GSF sells. Partly hidden by the clutch cables rubber support bung on the engine side. And it's added before painting the body shell. All August 1989 production onwards but not listed as a retro repair part. Therefore all GT11 & Scala Injections from G plate mid plate year onwards, ie. about Jan 1990 onwards. The plate is fixed on with adhesive. The early plate for August 1989/ July 1990 production was as the picture. Post August 1990 it was much smaller, being hidden under the rubber-seating bung of the clutch cable. If the cable pulls through the bulkhead, it’s usually a sign of a clutch very near the end of it’s life as the VW clutch mechanism gets heavier as the friction plate wears. .
-
Fairly common, always a carb engine in the UK, 1800cc Yes there were quite a few C auto's made with two types of box.
-
Sign of dirty oil. Not unusual if the engine is up past 75k miles. Sometimes helps to put in an engine oil flush additive just before the service and run for 50 miles. Then make oil changes more frequent than 10K. If you haven't oil pressure meter fitted, suggest it's checked sometime. Idle when fully warm - 95' to 98'C oil temp, should be 2 bar; 3,000 rpm 3.5 to 4 bar with 15W40 in the sump. .
-
That's the clutch pulling thro' the bulkhead. Being a GT11 it's already modified at the factory with a little lip plate on the engine side of the bulkhead on the lower half of the clutch cable hole on the engine. Throttle stiffness - check the whole cable, the radius of any turns should be gentle and be 2 foot radius or above otherwise there will be binding. If not that, change the cable. This is not a common problem with the Mk2 S, something about how the cable is routed is wrong.
-
Poor performance - CHeck the timing hasn't been retarded for unleaded petrol - ie TDC. Timing mark is the v notch in the flywheel (6'TBC) and should line up with the pointer dropping down on the engine side of the timing hole in the gearbox bell housing. TBC is referenced by a notch on the pulley at the bottom end of the engine on the offside (cambelt side) lining up with an impression mark in the plastic side cover. Brakes, can be sorted by adjusting the brake pedal push rod (under the driver's side of dash - drop the under dash cover to access ) two turns to take up the slack between the pedal and brake bell cranks) but check the brakes remain free after adjusting, ie. the brake pressure can still relieve back to the master cylinder on pedal release. Handbrake to 3 notches for full hard on. Again check the rear brakes free fully on release. If it's the original Peirburg Carb and the car is above 80K miles, think about a Weber replacement. (£250) Split petrol tanks, lip edge either side just in line with the front edge of the rear tyres. If OK get in (bad access, really needs the tank dropping which means the back axle needs to be dropped as well) and rust proof the area with Kurust and then use a liquid underseal like Supertrol 001) and regualarly inspect once a year. (New tank £230 + fitting) Petrol filler down pipe in the rear offside wheel arch corrodes filling the tank and fuel pipes with little rusty bits. Check, if OK, rust proof paint after wire brushing with something like Kurust and then lacquer paint on top with waxoyl on top of that. .
-
Get your man to check the lambda probe is operating by checking Measuring Blocks (08 ), group 001, field 3 The value should be somewhere between 0.95 and 1.05 at idle. Improtantly, it should be regularly changing slightly within the above range (about every 0.5 to 1 seconds). If it's stuck, usually 1.0 is indicated, it's goosed. This condition won't throw a fault code. But the exhaust will be stinky and rich.
-
As Gavin says, not the ECU, they're too robust. More a broken wire or sensor. Which why diagnostics is needed. TB set-up is an outsider in the stake of things at the mo (Gavin, seen the note, do later. Last time I did one it was very embarrassing, the owner almost killed me! A woman's scorn is very painful, particularly in public.) I'm guessing but the engine cuts out cos the ECU see's a condition it doesn't like. ie. the rising rpm. Something is telling the ECU to driving the throttle condition or broken wire has caused an imbalanced condition. No ISV, throttle body does all the work. Edit: Just thumbed thro’ my VAG pocket encyclopaedia………… Chris .
-
Doesn't exist in any Corrado ECU. Software is just locking up cos there will be no ECU response. Sounds like Snap-On haven't written the code to cope with no response correctly. Only fault codes (02), measuring blocks (08 ), basic settings (04), output tests (03) & login (11) exist. Adaption (10) is not facilitated. Yip! Always nice to have, it's 15 inches wide consisting of 18 volumes and not a Haynes. :) .
-
That could be a separate problem with the ignition switch. Pity no VAG-COM as the ECU does the throttle adjustment. Something is telling it to raise the RPM. THe ECU & throttle have to be set up if the power is lost to the ECU but it doesn't usually genrate this fault, just runs rougher. .
-
ADY engine has a motorised throttle controlled by the ECU. Has the battery been disconnected just before this happened? Two things to do initially. - Check for a broken wire around the throttle body at it's 8 wire connector. - Look at the fault memory with VAG-COM if you can, looking for a sensor down. .
-
Take a look at the micro switch inside the driver's door handle. Not unknown for the switch to fail.
-
Karmann quote 97,521. This ties in with chassis number of about 97,408, given the difference may be non roadworthy test cars etc. (There is an automatic VR6 prototype in the UK (LHD) which was supposed to have been scrapped at the factory. Came to light cos the car's wiring didn't match the wiring diagrams and the dealership couldn't resolve the owner's problem. VAG UK attempted to buy the car back!)
-
There's a vibration harmonic in the shaft but in practice it isn't nocticable. Sure it's loose? If solid on the shaft, leave alone.